STONE CRUSHER
Stone Crusher (also known as Rock Crusher) is a mechanical comminution device engineered to fragment large blocks of natural rock (e.g., granite, basalt), metallic ores (e.g., iron ore, copper ore), or recycled aggregates (e.g., construction debris, concrete rubble) into smaller, controlled particle sizes. Utilizing high-intensity mechanical stress—such as compression, impact, shearing, or attrition—it achieves particle size reduction to meet target granulometry specifications (typically 5–150 mm), ensuring physical compatibility with downstream processes like screening, grinding, calcination, or direct engineering applications. Core functional components include a power transmission system (electric motor/diesel engine-driven), a crushing chamber (equipped with dynamic/static liners or rotor-impact plate configurations), hydraulic/spring-based overload protection mechanisms, and particle size control modules (adjustable discharge openings, screening grids, or pre-screening systems). Designed for industrial applications, it facilitates material processing across mineral extraction, construction aggregate production, and waste recycling by optimizing mechanical force application and operational efficiency.
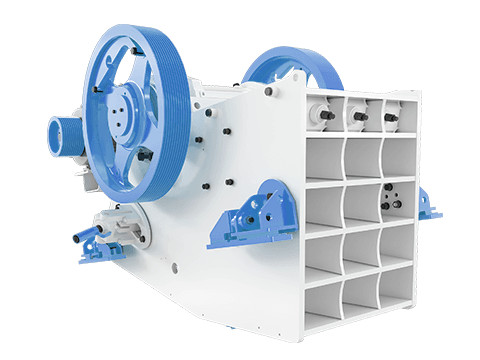
Jaw Crusher
Compressive Crushing: Utilizes compressive force generated by a reciprocating motion between a fixed jaw plate and a movable jaw plate. The material is crushed by progressive compression as it moves downward through the crushing chamber.
Learn more >>
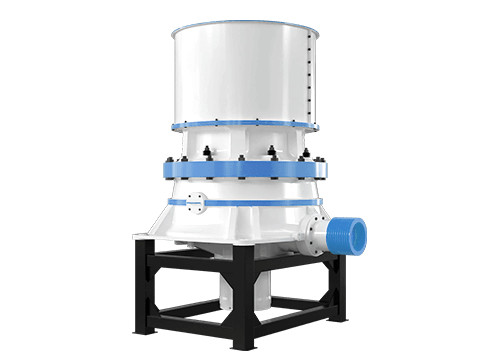
Cone Crusher
Employs interparticle crushing (also called layer compression), where rocks are crushed between a rotating mantle and a concave liner. The eccentric gyratory motion of the mantle creates a compressive force field, inducing fractures along grain boundaries.
Learn more >>
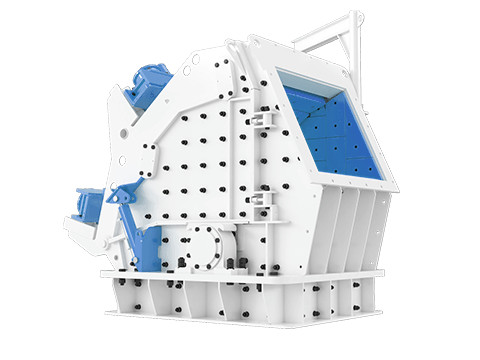
Impact Crusher
Dynamic Impact Crushing: Relies on kinetic energy transfer via high-speed rotors equipped with blow bars or hammers. Material is shattered by direct impact against rotating components or stationary anvils, with secondary fragmentation occurring through particle-on-particle collisions.
Learn more >>
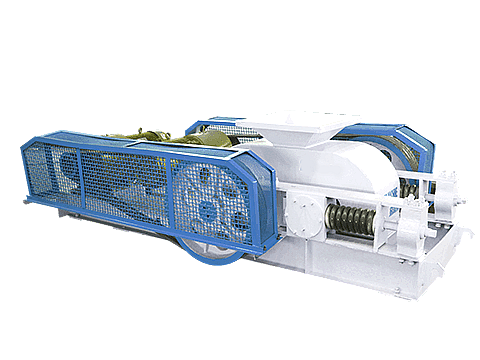
Roll Crusher
Shear-Compression Crushing: Applies shear-compression forces between counter-rotating rolls with textured or smooth surfaces. Material is drawn into the gap (nip angle) and fragmented via tensile failure or surface abrasion.
Learn more >>
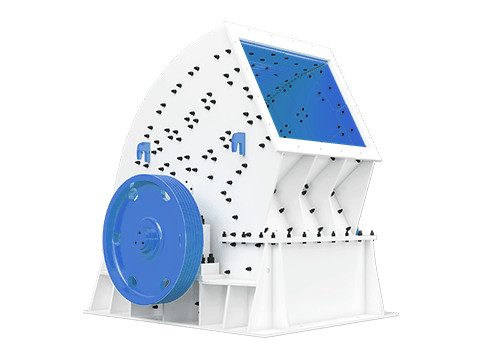
Hammer Crusher
Dynamic Impact with Grinding: Combines high-velocity hammer strikes (rotating hammers on a horizontal shaft) with material grinding against breaker plates or screens. Fragmentation occurs through impact, attrition, and shear.
Learn more >>
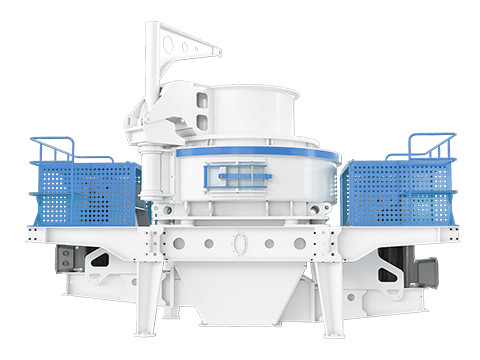
VSI Crusher
Centrifugal Acceleration Crushing: Accelerates material through a high-speed rotor (up to 70 m/s) and projects it against a stationary anvil or rock-lined chamber, exploiting centrifugal force and interparticle collision for fragmentation.
Learn more >>
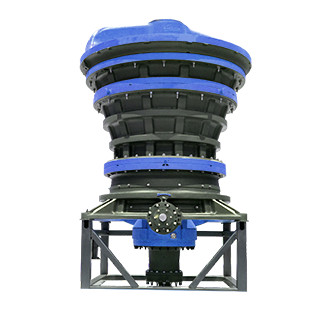
Gyratory Crusher
Conical Compression Crushing: Operates via a conical head gyrating within a concave bowl, generating progressive compression as material moves downward. Combines elements of jaw and cone crushers for ultra-high-capacity primary crushing.
Learn more >>
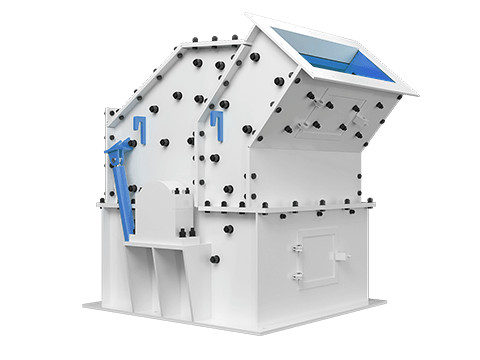
Fine Crusher
Fine Crusher is engineered for reliable and stable operation, making it an ideal choice for fine crushing applications across various industries.
Learn more >>
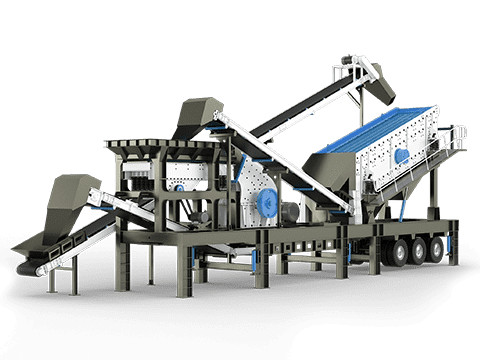
Mobile Crusher
The Mobile Crusher is designed to operate as a primary or secondary unit, making it a versatile choice for various applications.
Learn more >>
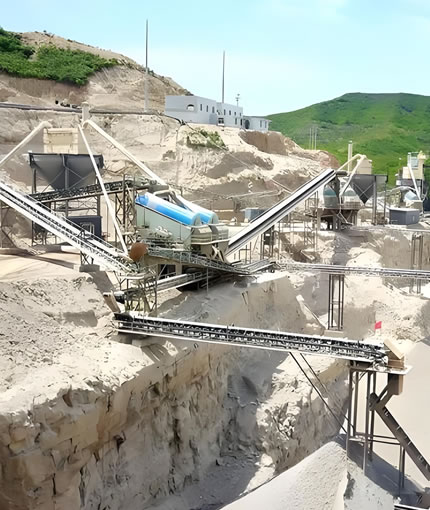
Mining and Quarrying
Our crushing solutions for mining and quarrying deliver high-performance equipment designed to handle the toughest materials, from hard rock to abrasive ores. With advanced jaw, cone, and gyratory crushers, we ensure efficient primary, secondary, and tertiary crushing for optimal mineral extraction and processing.
Learn more >>
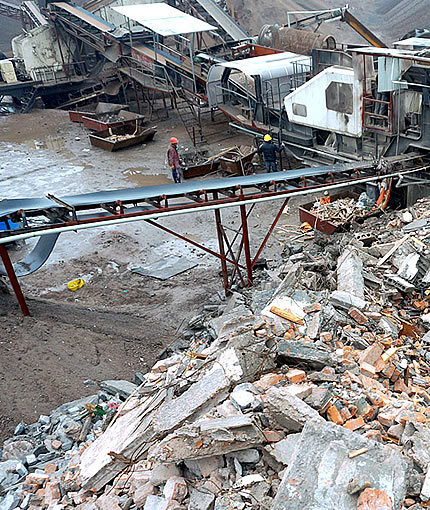
C&D Waste Recycling
Transform construction and demolition waste into valuable resources with our mobile and stationary crushing systems. Our solutions enable on-site recycling of concrete, bricks, and asphalt, reducing landfill use and promoting sustainable construction practices.
Learn more >>
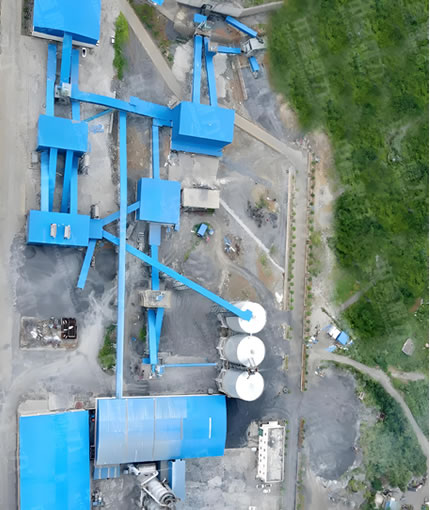
Aggregate Processing
From natural rock to recycled materials, our aggregate processing solutions produce high-quality sand, gravel, and crushed stone for construction projects. With precision crushing and screening, we ensure consistent gradation and superior particle shape for concrete and asphalt applications.
Learn more >>
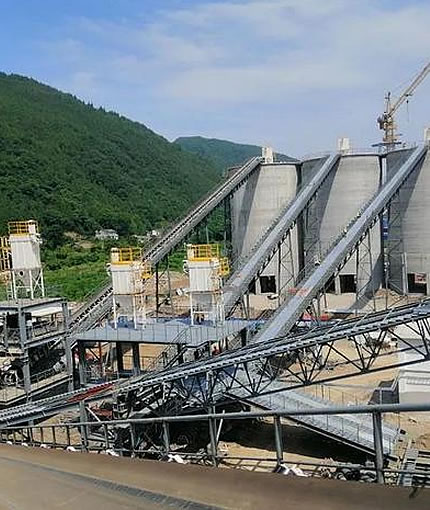
Cement Manufacturing
Optimize your cement production process with our crushing solutions tailored for limestone, clay, and other raw materials. Our robust crushers ensure uniform feed size, enhancing grinding efficiency and reducing energy consumption in cement manufacturing.
Learn more >>
Typical Three-Stage Stone Crushing Process
To produce high-quality aggregates, the following Three-Stage stone crushing process is commonly used:
- Primary Crusher → Crushes raw stones into 200mm - 400mm particles.
- Secondary Crusher → Reduces material size to 40mm - 100mm.
- Tertiary Crusher → Further crushes the material to 0-40mm or even finer.
Function: Handles the first stage of crushing, reducing large rocks into smaller pieces.
Common Types:
- Jaw Crusher – Suitable for hard and abrasive materials.
- Gyratory Crusher – Ideal for high-capacity applications.
- Impact Crusher – Sometimes used for softer stones like limestone.
Features: Large feed size (500mm - 1500mm), high capacity, mainly used in mining and quarrying.
Function: Further reduces the size of materials after primary crushing, ensuring uniform particles.
Common Types:
- Cone Crusher – Excellent for hard and medium-hard materials.
- Impact Crusher – Used when shaping is required.
- Roll Crusher – For medium-hard and brittle materials.
Features: Handles feed sizes of 100mm - 400mm, produces well-shaped aggregates.
Function: Provides final crushing to refine material into fine particles, often used for sand production.
Common Types:
- VSI Crusher – Used for producing high-quality manufactured sand.
- Fine Crusher – Further refines aggregates.
- High-Efficiency Cone Crusher – Provides finer crushing results.
Features: Handles 20mm - 100mm feed size, improves final product quality.
How to Choose the Right Stone Crusher?
Selecting the right stone crusher is critical for optimizing your crushing operations. Key factors to consider include crushing ratio, feed size, discharge size, and crushing capacity. The crushing ratio (the ratio of feed size to discharge size) determines the efficiency of size reduction, with higher ratios ideal for multi-stage crushing. Ensure the crusher can handle your maximum feed size while delivering the desired discharge size for downstream processes. Additionally, evaluate the crushing capacity (measured in tons per hour) to match your production requirements. For example, jaw crushers excel in primary crushing with high reduction ratios, while cone crushers are perfect for secondary crushing with precise discharge control. By aligning these parameters with your material type (e.g., granite, limestone) and application (e.g., mining, construction), you can maximize efficiency and minimize operational costs. Choose wisely to boost productivity and achieve optimal results in your crushing plant.
Crusher Type | Advantages | Disadvantages | Application | Suitable Materials | Output Size |
---|---|---|---|---|---|
Jaw Crusher | Simple structure, durable, easy maintenance, suitable for primary crushing | Large output size, requires secondary crushing, low efficiency | Mining, construction, metallurgy | Granite, basalt, ores | 100-300mm |
Cone Crusher | High crushing efficiency, good particle shape, less wear, suitable for secondary and fine crushing | Complex structure, high cost, not suitable for sticky materials | Mining, sand production | Granite, pebbles, iron ore | 5-50mm |
Impact Crusher | Large crushing ratio, uniform output size, suitable for medium-hard materials | Fast wear of parts, not suitable for high-hardness materials | Building materials, mining, metallurgy, chemicals | Limestone, concrete, coal | 10-50mm |
Hammer Crusher | Simple structure, one-time forming, high crushing ratio | High wear parts consumption, limited application range | Medium-hard and brittle materials | Coal, gypsum, limestone | 5-50mm |
Mobile Crusher | High mobility, suitable for on-site operations, saves transportation costs | Limited processing capacity, high cost | Construction waste, mining, road engineering | Various materials | 5-100mm |
Fine Crusher | High efficiency, small output size, suitable for sand production | High energy consumption, relatively low output | Sand making, building materials | Limestone, pebbles, granite | 0-5mm |
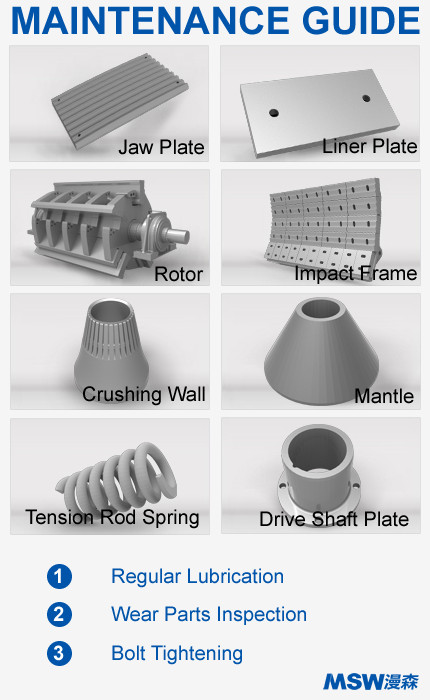
Essential Tips for Maintaining Your Stone Crusher
Proper maintenance of your stone crusher is crucial for ensuring long-term performance and minimizing downtime. Start by regularly inspecting the crushing chamber for wear and tear, as damaged jaw plate, mantle, or concave can reduce efficiency and increase energy consumption. Replace worn crusher liner plate and blow bar promptly to maintain optimal crushing force and particle size control. Check the toggle plate for cracks and ensure the eccentric shaft is properly lubricated to prevent overheating. Additionally, monitor the rotor and hammer head for balance and wear, especially in impact crushers. Don’t forget the flywheel, which helps stabilize the crusher’s operation—ensure it’s free of debris and securely fastened. By following these maintenance practices, you can extend the lifespan of your stone crusher, improve crushing capacity, and reduce operational costs. Regular upkeep not only enhances performance but also ensures safety and reliability in your crushing operations.
Why choose us
Customized crusher with reliable price
We offer more than just stone crushers—we provide complete solutions tailored to your specific needs. With years of experience in the industry, we have developed cutting-edge technology and engineering expertise to deliver reliable, high-performance crushers that are built to last. Our commitment to quality and innovation ensures that you receive equipment that maximizes efficiency, minimizes downtime, and reduces operational costs.
Contact Us
Don't know how to choose? Need more detail? Contact us to provide you with customized services. Our specialist will be at your service.