Hammer Crusher
Hammer crusher, as the name implies, is a mechanical device that uses high-speed rotating hammers to impact, shear, grind and other effects on materials to achieve material crushing. It has a simple structure, large crushing ratio and high production efficiency. It is widely used in mining, metallurgy, building materials, chemical industry and other industries to crush limestone, coal gangue, gypsum and other medium-hard and lower materials.
Main Components of Hammer Crusher
Hammer Crusher Types
Maintenance of Hammer Crushers
Regular Inspection of Hammer and Rotor
Routine inspection of the hammer and rotor is critical to maintaining the performance of the hammer crusher. Over time, hammers can wear down due to continuous impact with materials. Checking for cracks, wear, and misalignment helps prevent more serious damage and ensures optimal crushing efficiency.
Lubrication of Bearings and Rotating Parts
Proper lubrication of the bearings and other rotating parts of the hammer crusher is essential for reducing friction and wear. Regularly checking and replenishing the lubricant prevents overheating and extends the life of key components, ensuring smooth operation and minimizing downtime.
Cleaning of Crusher Components
Cleaning the crusher’s internal components, such as the hammers, grates, and rotor, helps remove accumulated dust and debris that can impact performance. Regular cleaning also helps in identifying early signs of wear and tear, ensuring that components are in good working condition.
Monitoring Vibration and Noise Levels
Excessive vibration or abnormal noise during operation can indicate mechanical issues such as imbalance or wear in the rotor. Monitoring vibration and noise levels can help detect problems early, allowing for timely repairs and preventing further damage to the crusher.
Checking and Replacing Screens and Grates
Over time, the screens and grates in a hammer crusher may become worn or clogged with material. Regular inspection and replacement of these components ensure that material flow remains consistent and that the crusher produces the desired particle size efficiently.
Adjusting the Feed and Discharge Ports
Proper adjustment of the feed and discharge ports helps maintain consistent crushing performance. Over time, wear on the crusher's components may cause misalignment, which can lead to irregular material output. Periodic adjustments ensure the crusher continues to perform at its best.
Ensuring Proper Tightening of Bolts and Fasteners
The high-impact forces generated during crushing can loosen bolts and fasteners over time. Regular checks for tightness and re-tightening as necessary ensure the stability of the crusher and prevent operational failures due to loose components.
Replacement of Worn or Damaged Hammers
Hammers are critical components in a hammer crusher and are subjected to significant wear during operation. Regular monitoring and timely replacement of worn or damaged hammers prevent poor performance, material blockages, and potential damage to other parts of the crusher.
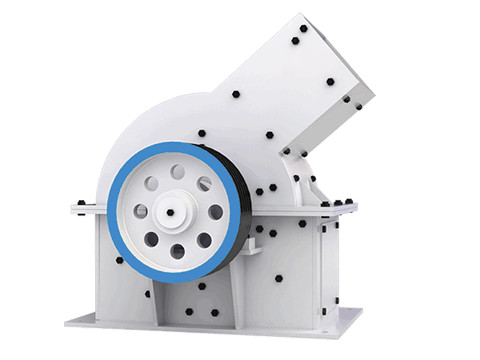
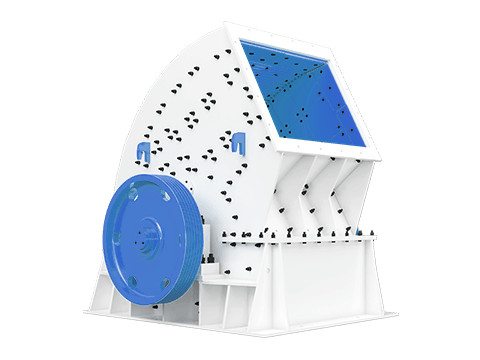
Applications of Hammer Crushers
Crushing of Soft to Medium-Hard Materials
Hammer crushers are commonly used for crushing soft to medium-hard materials such as limestone, coal, gypsum, and shale. These crushers are highly effective at breaking down large volumes of material quickly, making them ideal for applications in mining, cement production, and power generation.
Production of Fine Aggregates
Hammer crushers are utilized in aggregate production to generate fine crushed material. The high impact force of the hammers allows for the reduction of large rocks into smaller, uniform particle sizes, which are ideal for use in construction, road building, and concrete production.
Recycling of Construction and Demolition Waste
In the recycling industry, hammer crushers are often employed to break down construction and demolition waste, such as concrete, bricks, and asphalt. This process helps to recover valuable materials for reuse, reducing the environmental impact of waste disposal and promoting sustainability.
Crushing of Organic Materials
Hammer crushers are also used in the processing of organic materials, such as wood, biomass, and agricultural waste. These materials are crushed into smaller particles for use in energy generation, animal bedding, or composting applications.
Coal Preparation in Power Plants
Hammer crushers play a crucial role in the preparation of coal for combustion in power plants. They break down larger coal chunks into smaller, uniform sizes, ensuring that the coal burns efficiently and evenly in the furnace, improving energy production and reducing emissions.
Crushing of Fertilizers and Chemicals
In the chemical and fertilizer industries, hammer crushers are used to crush raw materials like minerals, chemicals, and fertilizers into fine powders. This allows for better blending and mixing of the materials before they are used in production processes or distributed to consumers.
Processing of Metal Scraps
Hammer crushers are effective in processing scrap metal, including aluminum, copper, and steel. By breaking down metal scrap into smaller pieces, hammer crushers help facilitate recycling and further processing of metals into usable forms for manufacturing and construction.
How to Choose the Right Hammer Crusher?
Choosing the right hammer crusher is essential for ensuring efficient material processing, reducing maintenance costs, and optimizing production output. With various models and specifications available, selecting the best hammer crusher requires a thorough understanding of material characteristics, production capacity, and operational requirements. A well-chosen hammer crusher enhances productivity, minimizes downtime, and improves overall cost-effectiveness. This article explores the key factors to consider when selecting a hammer crusher for your specific needs.
Understanding Material Properties
The type of material to be processed plays a crucial role in selecting the right hammer crusher. Factors such as hardness, moisture content, and abrasiveness determine the crusher’s performance and wear resistance. Hammer crushers are well-suited for crushing soft to medium-hard materials like limestone, gypsum, coal, and shale. For highly abrasive or harder materials, selecting wear-resistant hammer heads and liners is necessary to extend equipment lifespan.
Determining Production Capacity
The required production capacity is an important factor in choosing a hammer crusher. Selecting a crusher with the appropriate rotor speed, hammer configuration, and power ensures it can handle the required throughput without causing operational bottlenecks. Underestimating capacity can lead to inefficient processing, while overestimating can result in unnecessary energy consumption and higher costs.
Evaluating Feed Size and Output Requirements
The size of the input material and the desired final product size influence the choice of a hammer crusher. A larger feed opening allows the crusher to handle bigger raw materials without the need for pre-crushing. Additionally, adjustable grate bars or screen plates help control the output size, ensuring that the final product meets specific requirements for further processing or direct use.
Considering Rotor Design and Hammer Configuration
The rotor is the heart of a hammer crusher, and its design impacts crushing efficiency. Different rotor speeds and hammer arrangements affect how materials are broken down. High-speed rotors generate greater impact force, improving material reduction, while adjustable hammer positioning enhances versatility. Some models also feature reversible hammers, which extend service life and reduce maintenance costs.
Energy Efficiency and Power Consumption
Energy efficiency is a key factor in selecting a hammer crusher. Opting for a model with optimized power consumption can significantly lower operational costs. Modern hammer crushers often incorporate energy-saving features such as variable-speed drives and automated control systems, which improve efficiency and reduce overall electricity usage.
Durability and Maintenance Considerations
Durability is essential for long-term cost-effectiveness. A well-constructed hammer crusher with high-quality wear-resistant materials ensures a longer operational lifespan and minimizes downtime. Features such as replaceable hammers, easy-access maintenance points, and hydraulic opening systems simplify maintenance and improve overall operational efficiency.
Comparing Different Hammer Crusher Models
Manufacturers offer a variety of hammer crushers designed for different applications. Comparing models based on factors such as rotor speed, crushing chamber design, and hammer material helps in selecting the most suitable crusher. Some advanced models come with automation features, allowing real-time monitoring and adjustments to optimize performance.
Choosing a Reliable Manufacturer and Supplier
Working with a trusted manufacturer or supplier ensures access to high-quality equipment, reliable technical support, and genuine spare parts. A reputable supplier provides guidance in selecting the right hammer crusher for specific applications and offers after-sales services to ensure long-term operational success.
Making an Informed Decision
Selecting the right hammer crusher requires a careful assessment of material characteristics, production needs, energy efficiency, and durability. By considering these factors, businesses can invest in a crusher that enhances productivity, reduces maintenance costs, and ensures efficient material processing. A well-chosen hammer crusher is a valuable asset for industries such as mining, construction, and recycling, delivering consistent and reliable performance over time.
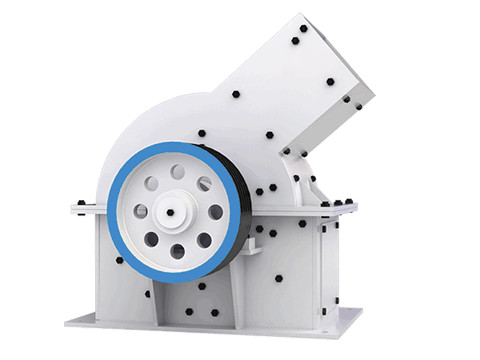
Stone Crusher Types
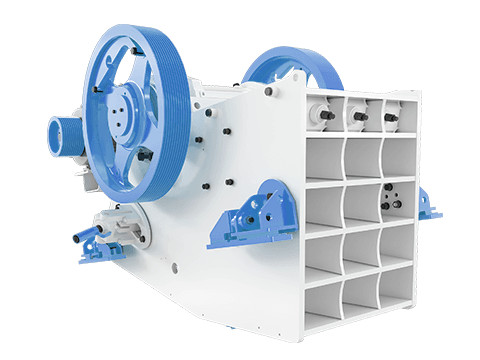
Jaw Crusher
Compressive Crushing: Utilizes compressive force generated by a reciprocating motion between a fixed jaw plate and a movable jaw plate. The material is crushed by progressive compression as it moves downward through the crushing chamber.
Learn more >>
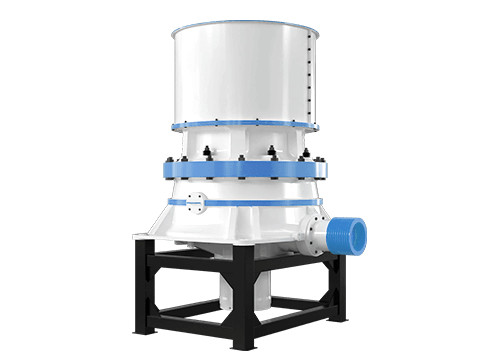
Cone Crusher
Employs interparticle crushing (also called layer compression), where rocks are crushed between a rotating mantle and a concave liner. The eccentric gyratory motion of the mantle creates a compressive force field, inducing fractures along grain boundaries.
Learn more >>
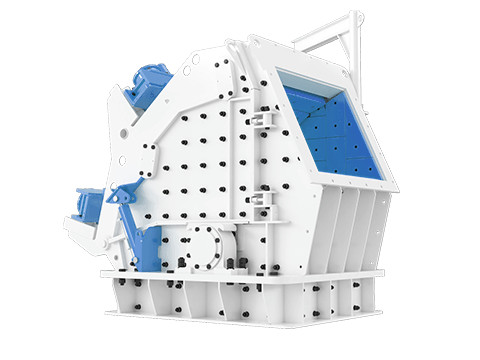
Impact Crusher
Dynamic Impact Crushing: Relies on kinetic energy transfer via high-speed rotors equipped with blow bars or hammers. Material is shattered by direct impact against rotating components or stationary anvils, with secondary fragmentation occurring through particle-on-particle collisions.
Learn more >>
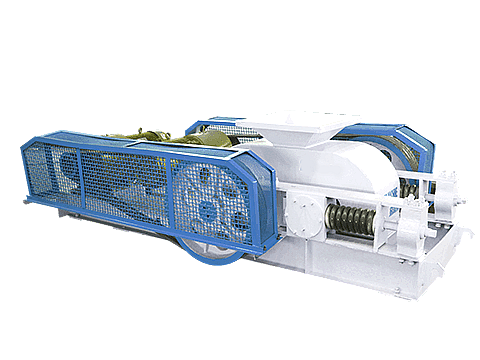
Roll Crusher
Shear-Compression Crushing: Applies shear-compression forces between counter-rotating rolls with textured or smooth surfaces. Material is drawn into the gap (nip angle) and fragmented via tensile failure or surface abrasion.
Learn more >>
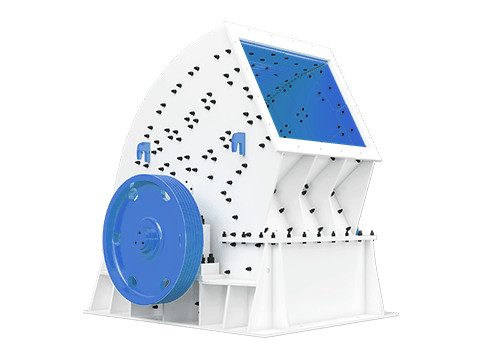
Hammer Crusher
Dynamic Impact with Grinding: Combines high-velocity hammer strikes (rotating hammers on a horizontal shaft) with material grinding against breaker plates or screens. Fragmentation occurs through impact, attrition, and shear.
Learn more >>
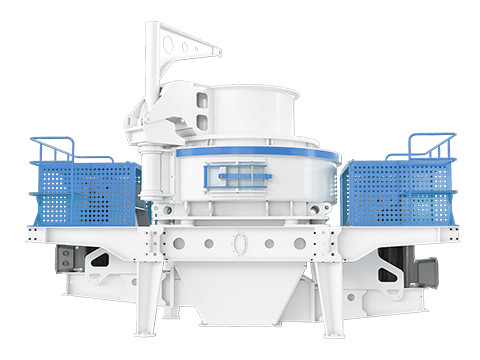
VSI Crusher
Centrifugal Acceleration Crushing: Accelerates material through a high-speed rotor (up to 70 m/s) and projects it against a stationary anvil or rock-lined chamber, exploiting centrifugal force and interparticle collision for fragmentation.
Learn more >>
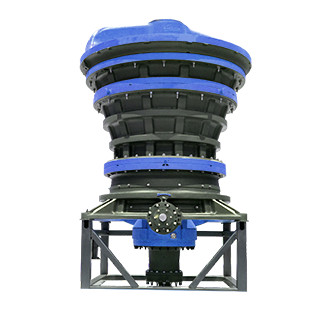
Gyratory Crusher
Conical Compression Crushing: Operates via a conical head gyrating within a concave bowl, generating progressive compression as material moves downward. Combines elements of jaw and cone crushers for ultra-high-capacity primary crushing.
Learn more >>
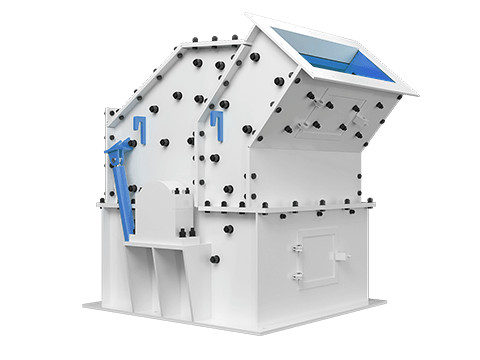
Fine Crusher
Fine Crusher is engineered for reliable and stable operation, making it an ideal choice for fine crushing applications across various industries.
Learn more >>
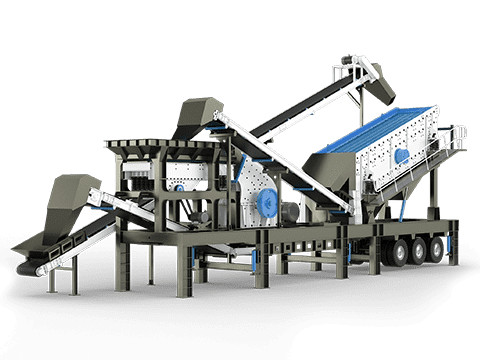
Mobile Crusher
The Mobile Crusher is designed to operate as a primary or secondary unit, making it a versatile choice for various applications.
Learn more >>