Mobile Crusher
Mobile crushers are advanced crushing machines designed for on-site material processing, offering high mobility and flexibility. Unlike stationary crushers, they can be easily transported between job sites, making them ideal for construction, mining, and recycling applications.
There are different types of mobile crushers, including mobile jaw crushers for primary crushing, mobile cone crushers for secondary and fine crushing, and mobile impact crushers for producing high-quality aggregates. Mobile VSI crushers specialize in shaping and sand production.
With features like remote control operation, efficient fuel consumption, and quick setup, mobile crushers improve productivity while reducing transportation costs. Their adaptability to various environments makes them essential for modern material processing operations.
Mobile Crusher Types
Maintenance of Mobile Crusher
Regular maintenance of mobile crushers is essential for ensuring optimal performance, preventing unexpected breakdowns, and extending the lifespan of the equipment. Proper upkeep minimizes downtime and helps maintain consistent crushing efficiency in demanding environments.
Regular Inspections of Key Components
Regularly inspecting key components like the engine, tracks, and crushing chamber is crucial to detect any wear, misalignment, or potential issues. This helps in addressing problems before they lead to major breakdowns.
Cleaning and Removing Material Build-up
Over time, material can accumulate in various parts of the mobile crusher, especially in the feeding area and discharge belt. Periodically cleaning these areas ensures smooth material flow and prevents blockages.
Lubrication of Moving Parts
Proper lubrication of the bearings, shafts, and other moving parts is essential to minimize friction, reduce wear, and prevent overheating. Using the right lubricants and maintaining regular lubrication intervals is vital for efficient operation.
Checking and Replacing Wear Parts
Wear parts like jaw plates, impact bars, and screens should be regularly inspected for signs of wear and replaced when necessary. Timely replacement ensures that the crusher operates efficiently and minimizes the risk of more significant damage.
Examining Hydraulic Systems
Mobile crushers often use hydraulic systems for adjusting settings and controlling functions. Regular inspection of the hydraulic components, such as hoses, pumps, and cylinders, ensures they remain in optimal condition and free of leaks.
Monitoring and Maintaining Engine Health
The engine is the heart of a mobile crusher, and regular monitoring of its performance, including checking fuel levels, filters, and air intake systems, is critical. Keeping the engine in good health helps prevent power loss and fuel inefficiency.
Ensuring Proper Alignment and Adjustment of the Crusher
Misalignment of the crusher components, such as the rotor or crushing chamber, can lead to inefficient operation and increased wear. Regularly checking and adjusting the alignment ensures smooth and accurate crushing performance.
Checking and Maintaining Electrical Systems
The electrical systems that control the crusher’s operation should be regularly tested to ensure proper functioning. This includes checking wiring, connections, and control panels for any faults or damage.
Inspecting Tracks and Tires
The tracks or tires that provide mobility for the crusher should be inspected for wear, cracks, and damage. Ensuring they are in good condition helps maintain proper mobility and prevents unexpected disruptions in the operation.
Adhering to a Preventive Maintenance Schedule
Implementing a preventive maintenance schedule helps in identifying and addressing minor issues before they turn into significant problems. Regular maintenance intervals based on manufacturer recommendations ensure the crusher operates at peak performance throughout its life.
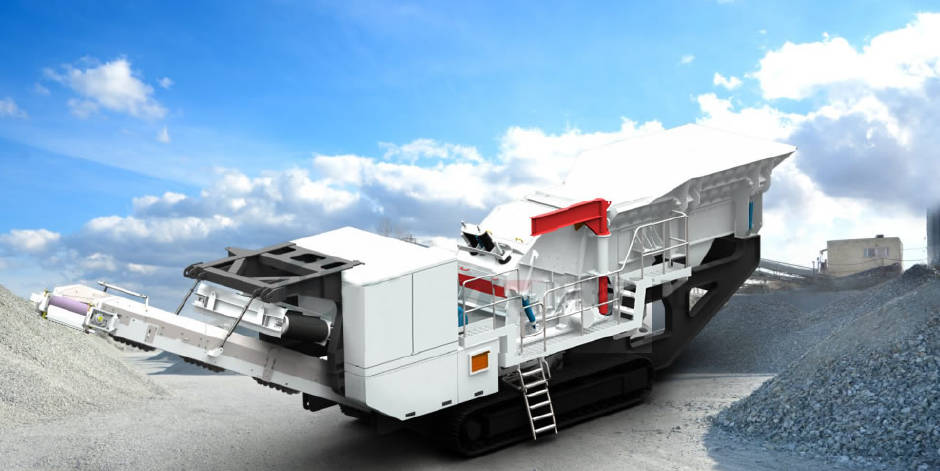
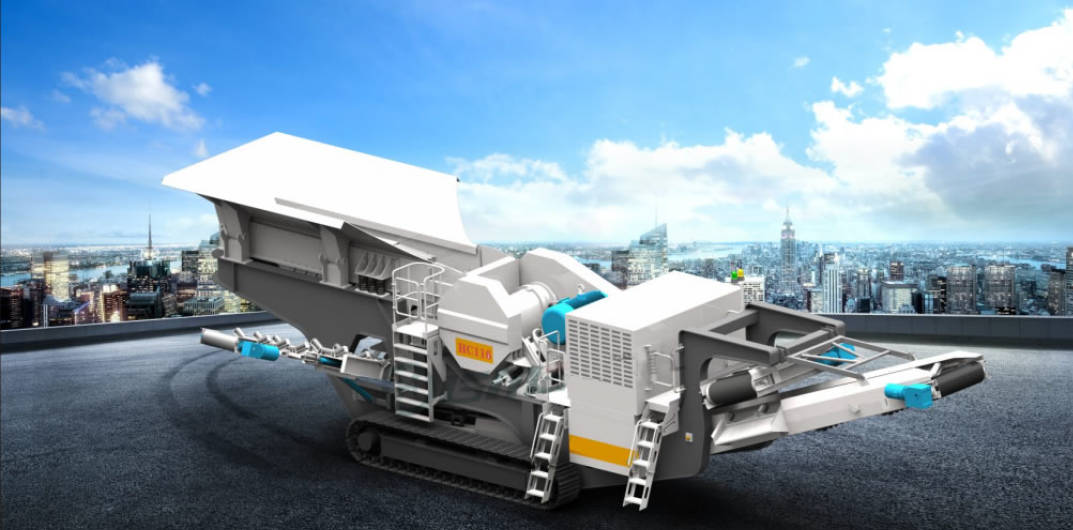
Applications of Mobile Crusher
Mobile crushers are versatile machines used in various industries for on-site material processing and recycling. Their portability and flexibility make them ideal for applications that require mobility and efficient crushing in remote locations or on construction sites.
Construction and Demolition Waste Recycling
Mobile crushers are widely used in construction and demolition projects to recycle materials such as concrete, bricks, and asphalt. These crushers can be set up directly on-site, reducing transportation costs and enabling the reuse of materials for new construction projects.
Mining and Quarrying
In mining and quarrying operations, mobile crushers are used for primary and secondary crushing. They provide a cost-effective solution for extracting and processing minerals, ores, and aggregates, especially in locations with limited access to traditional crushing plants.
Road Construction
Mobile crushers are commonly used in road construction to process materials like sand, gravel, and asphalt. They enable efficient production of aggregate materials and allow for the construction of roads in remote areas where traditional infrastructure may not be available.
Recycling of Asphalt and Concrete
Mobile crushers are essential in recycling old asphalt and concrete materials into reusable aggregates. This process reduces waste and the need for virgin materials, contributing to more sustainable construction practices.
Environmental and Demolition Projects
Mobile crushers are used in environmental and demolition projects to break down large structures and process waste materials. Their ability to crush a wide range of materials makes them essential for clearing debris and preparing sites for future use.
Aggregate Production for Manufacturing
Mobile crushers are employed in aggregate production, where they help process raw materials like sand, gravel, and crushed stone. These aggregates are used in manufacturing concrete, asphalt, and other construction products.
Landscaping and Site Preparation
Mobile crushers are often used for site preparation and landscaping work, including breaking down rocks, boulders, and other materials that are too large to be processed by traditional machinery. This helps in clearing land for construction or other uses.
Demolition of Bridges and Other Infrastructure
In large-scale demolition projects, such as the dismantling of bridges or old buildings, mobile crushers are employed to crush and process materials on-site. This helps reduce transportation costs and makes the demolition process more efficient.
How to Choose the Right Mobile Crusher?
Choosing the right mobile crusher is essential for optimizing material processing efficiency, reducing operational costs, and ensuring flexibility in various work environments. Several factors must be considered, including material type, capacity, mobility, and operational requirements.
Understanding the Material Characteristics
The hardness, moisture content, and abrasiveness of the material to be processed play a crucial role in selecting the right mobile crusher. Harder materials may require jaw or cone crushers, while softer materials can be efficiently processed with impact crushers.
Evaluating Capacity and Production Requirements
Mobile crushers come in different capacities, and choosing the right one depends on the production needs. High-capacity crushers are ideal for large-scale projects, while compact models are suitable for small to medium operations.
Choosing the Right Crusher Type
Different mobile crushers serve different purposes. Jaw crushers are effective for primary crushing, cone crushers for secondary and fine crushing, and impact crushers for shaping and recycling applications.
Assessing Mobility and Transportability
The ease of transport and setup is a key consideration. Some mobile crushers are track-mounted for rough terrains, while others are wheel-mounted for improved maneuverability on paved surfaces.
Checking Fuel Efficiency and Power Source
Mobile crushers operate on diesel, electric, or hybrid power. Selecting an energy-efficient model can help reduce fuel consumption and operational costs.
Considering the Feed and Discharge Configuration
The crusher’s feeding and discharge system should match the operational requirements. A wider feed opening allows handling of larger materials, while adjustable discharge settings help achieve the desired product size.
Examining Automation and Control Features
Modern mobile crushers come with automated systems for real-time monitoring, load management, and remote control operation. These features enhance efficiency and reduce operator workload.
Reviewing Maintenance and Serviceability
Easy access to wear parts, simple lubrication systems, and minimal downtime for servicing are important factors when choosing a mobile crusher to ensure long-term operational efficiency.
Comparing Different Brands and Models
Manufacturers offer various mobile crusher models with different features. Comparing specifications, user reviews, and expert recommendations helps in making an informed decision.
Balancing Cost and Performance
While initial purchase cost is a factor, long-term operating costs, including fuel, maintenance, and replacement parts, should also be considered for the most cost-effective solution.
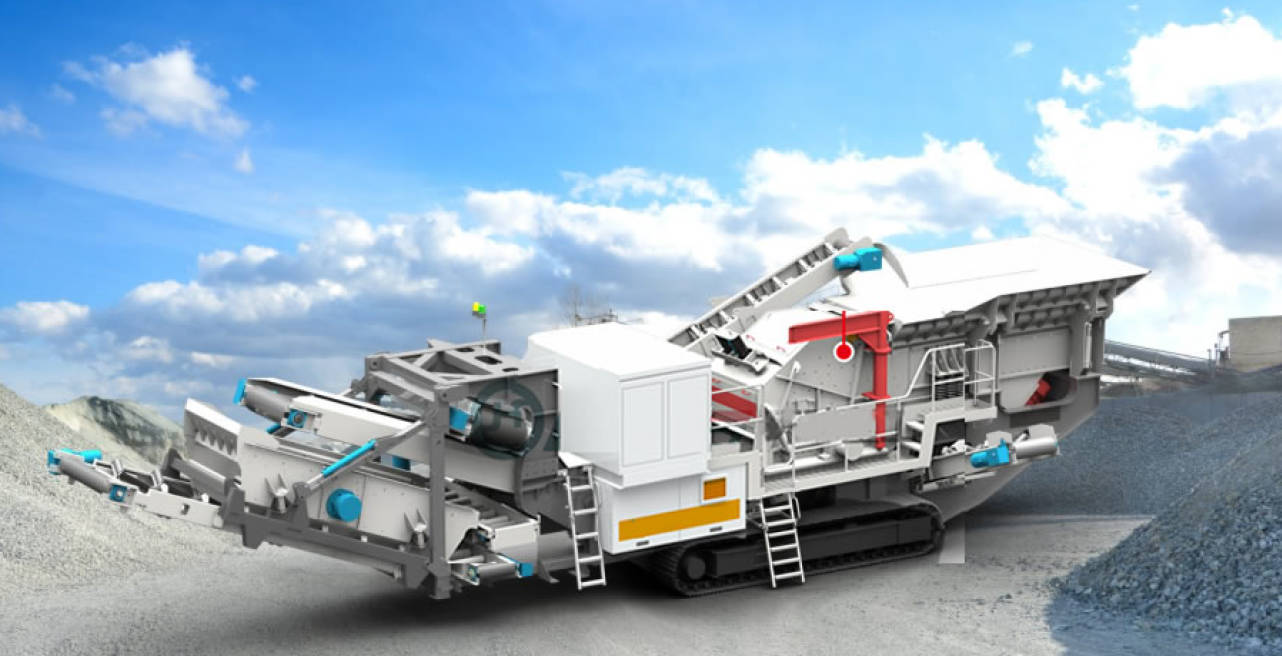
Stone Crusher Types
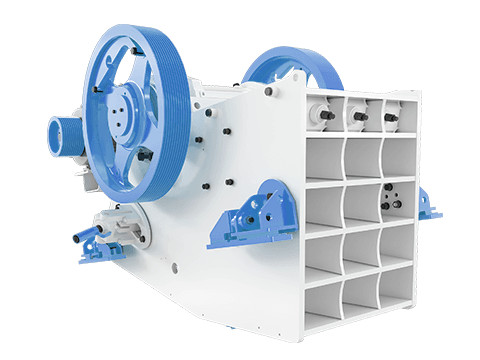
Jaw Crusher
Compressive Crushing: Utilizes compressive force generated by a reciprocating motion between a fixed jaw plate and a movable jaw plate. The material is crushed by progressive compression as it moves downward through the crushing chamber.
Learn more >>
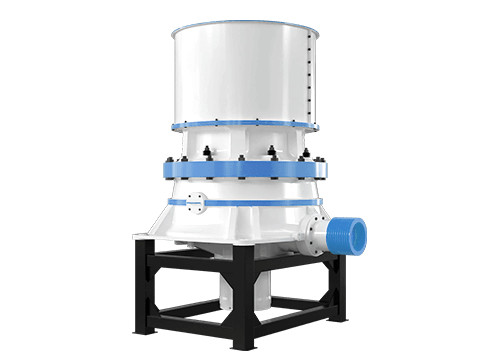
Cone Crusher
Employs interparticle crushing (also called layer compression), where rocks are crushed between a rotating mantle and a concave liner. The eccentric gyratory motion of the mantle creates a compressive force field, inducing fractures along grain boundaries.
Learn more >>
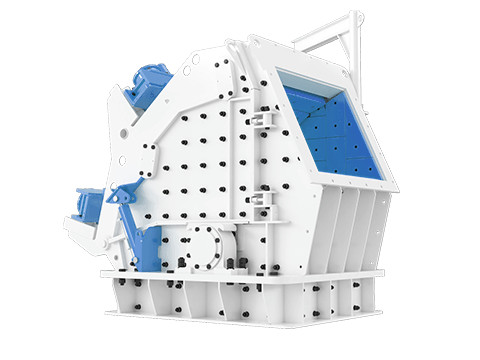
Impact Crusher
Dynamic Impact Crushing: Relies on kinetic energy transfer via high-speed rotors equipped with blow bars or hammers. Material is shattered by direct impact against rotating components or stationary anvils, with secondary fragmentation occurring through particle-on-particle collisions.
Learn more >>
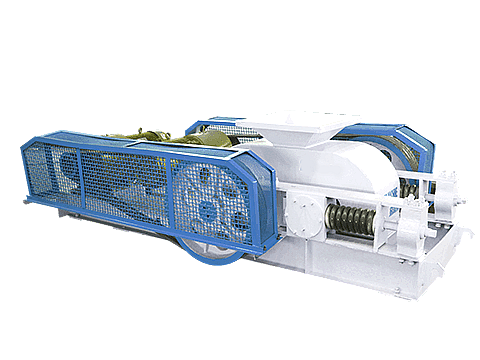
Roll Crusher
Shear-Compression Crushing: Applies shear-compression forces between counter-rotating rolls with textured or smooth surfaces. Material is drawn into the gap (nip angle) and fragmented via tensile failure or surface abrasion.
Learn more >>
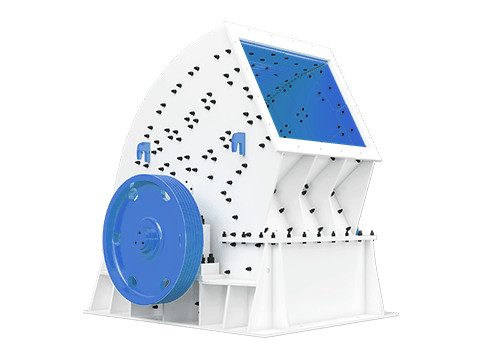
Hammer Crusher
Dynamic Impact with Grinding: Combines high-velocity hammer strikes (rotating hammers on a horizontal shaft) with material grinding against breaker plates or screens. Fragmentation occurs through impact, attrition, and shear.
Learn more >>
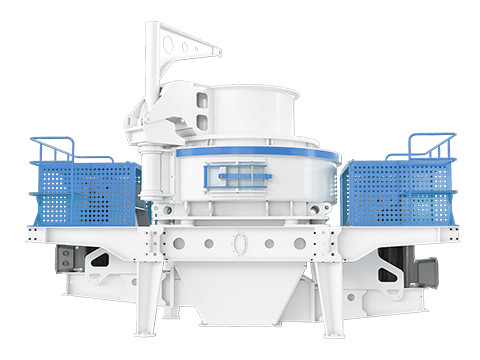
VSI Crusher
Centrifugal Acceleration Crushing: Accelerates material through a high-speed rotor (up to 70 m/s) and projects it against a stationary anvil or rock-lined chamber, exploiting centrifugal force and interparticle collision for fragmentation.
Learn more >>
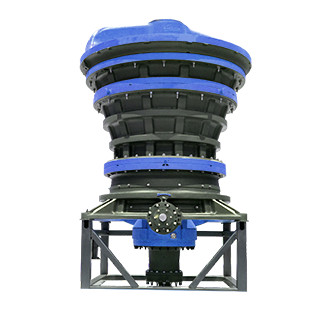
Gyratory Crusher
Conical Compression Crushing: Operates via a conical head gyrating within a concave bowl, generating progressive compression as material moves downward. Combines elements of jaw and cone crushers for ultra-high-capacity primary crushing.
Learn more >>
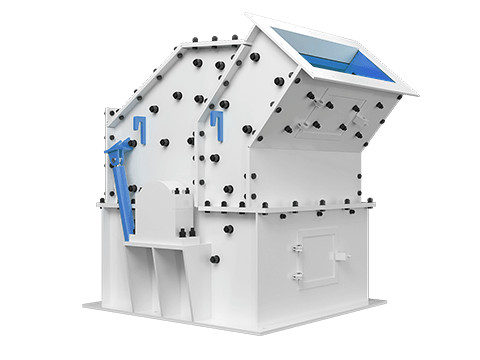
Fine Crusher
Fine Crusher is engineered for reliable and stable operation, making it an ideal choice for fine crushing applications across various industries.
Learn more >>
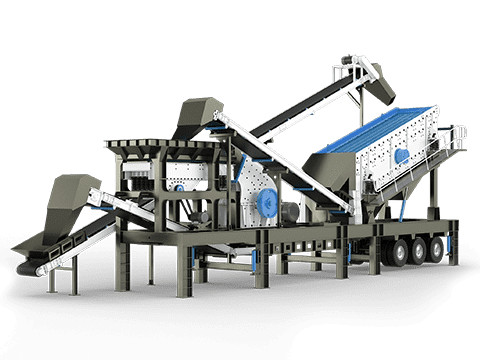
Mobile Crusher
The Mobile Crusher is designed to operate as a primary or secondary unit, making it a versatile choice for various applications.
Learn more >>