Fine Crusher
Fine Crusher is engineered for reliable and stable operation, making it an ideal choice for fine crushing applications across various industries. With a simplified structure and convenient maintenance, this crusher delivers high production capacity and a long service life for its hammer heads. It is widely used for crushing granite, basalt, limestone, river pebbles, cement clinker, quartz stone, iron ore, bauxite, and more.
Fine Crusher Types
Maintenance of Fine Crusher
Maintaining a fine crusher is essential for ensuring its longevity, optimal performance, and minimal downtime. Regular maintenance helps in preventing potential breakdowns, ensuring high efficiency and reducing overall operational costs.
Regular Inspection of Crusher Components
Frequent inspections of key components such as the rotor, wear plates, and bearings help identify any signs of wear or damage. This proactive approach prevents unexpected breakdowns and ensures the crusher operates smoothly.
Cleaning and Removing Material Build-up
Fine crushers can accumulate debris or material buildup in various parts, such as the feed inlet, discharge chute, and internal crushing chamber. Regular cleaning of these areas prevents blockages and ensures the efficient flow of materials.
Lubrication of Moving Parts
Proper lubrication of the bearings, shafts, and other moving parts is critical to minimizing friction and preventing excessive wear. Lubrication intervals should be followed as per the manufacturer’s recommendations to maintain smooth operation.
Checking and Replacing Wear Parts
Wear parts like the hammer head, liners, and screens should be regularly inspected for wear and replaced when needed. Timely replacement of these components ensures the fine crusher’s performance remains at its best.
Monitoring and Maintaining Electrical Systems
Electrical components, such as motors, wiring, and control panels, should be checked regularly for damage or malfunctions. Ensuring the electrical system is in good condition reduces the risk of unexpected shutdowns and improves operational reliability.
Examining Rotor and Crushing Chamber
The rotor and crushing chamber are critical parts of a fine crusher. These should be inspected for any damage or wear. Misalignment or irregularities in these areas can lead to inefficient crushing and increased wear on other parts.
Monitoring Vibration and Noise Levels
Excessive vibration or abnormal noise can indicate issues with the crusher's balance, rotor, or bearing system. Monitoring vibration and noise levels can help identify potential problems early, preventing further damage and reducing repair costs.
Checking and Adjusting Crusher Settings
Properly adjusting the crusher settings, such as the gap between the rotor and the liner, is essential to maintain product quality and crushing efficiency. Regular adjustments based on material properties ensure consistent results.
Ensuring Proper Cooling of Hydraulic Systems
If the fine crusher uses hydraulic systems, it’s crucial to monitor the temperature and ensure proper cooling. Overheating can lead to failure or damage to hydraulic components, resulting in increased maintenance and repair costs.
Following a Preventive Maintenance Schedule
Establishing and adhering to a preventive maintenance schedule based on the manufacturer’s recommendations helps in identifying potential issues early and reduces the likelihood of major failures, ensuring continuous and reliable performance.
Applications of Fine Crusher
Fine crushers are crucial in various industries for refining raw materials and producing desired particle sizes. Their versatility makes them ideal for a wide range of applications, from mining to construction and recycling.
Sand and Gravel Production
Fine crushers are extensively used in the production of sand and gravel for construction purposes. They ensure that the materials meet the required specifications for concrete, asphalt, and other construction applications.
Mineral Processing
In the mining industry, fine crushers play a key role in processing ores and minerals. They are used to crush raw minerals to a finer size for further processing in smelting, extraction, or refining operations.
Cement Production
Fine crushers are used in cement plants to reduce clinker and other materials to the required size. The finer particles enhance the quality of the cement, improving its performance in various construction applications.
Coal and Limestone Crushing
In power plants and steel industries, fine crushers are used to process coal and limestone. The crushed materials are used in various applications, such as in power generation and the production of lime for industrial processes.
Recycling of Construction and Demolition Waste
Fine crushers are employed in recycling operations to break down construction and demolition waste materials, such as concrete, bricks, and asphalt, into smaller particles for reuse in new construction projects.
Glass and Ceramic Material Processing
Fine crushers are used in the production of glass and ceramics, where fine crushing is required to process materials like silica, clay, and other raw ingredients into a fine powder or specific particle size.
Plastic and Rubber Recycling
In the recycling industry, fine crushers help process plastic and rubber waste into smaller, reusable particles. This contributes to reducing environmental impact and promoting sustainable waste management practices.
Food and Agricultural Products Processing
Fine crushers are used in the food industry to process grains, fruits, and other agricultural products into finer textures, ensuring consistency and quality in the final product.
Chemical and Fertilizer Production
Fine crushers are utilized in the chemical industry for processing raw materials into fine powders for use in various chemical reactions, as well as in the production of fertilizers for agricultural use.
Steel Manufacturing
In steel manufacturing, fine crushers are used to break down raw materials like iron ore into fine particles that are then used in blast furnaces to produce steel and other related products.
How to Choose the Right Fine Crusher?
Choosing the right fine crusher is essential to achieving the desired particle size, reducing operating costs, and ensuring the efficiency of the crushing process. Several factors need to be taken into account to ensure the fine crusher meets the specific requirements of the project.
Understanding the Material Characteristics
Before selecting a fine crusher, it is important to consider the material being processed. Factors like hardness, moisture content, abrasiveness, and particle size should all be considered. Harder and more abrasive materials may require crushers that are specifically designed for durability.
Defining Desired Particle Size
The desired output size plays a critical role in selecting the right fine crusher. Crushers such as hammer mills or impact crushers may be more suitable for finer particle sizes, while others like cone crushers may be better for coarser outputs.
Capacity Requirements
The required throughput or processing capacity is another important consideration. If the project requires a high volume of crushed material, choosing a fine crusher with a higher capacity ensures that production demands are met without overloading the equipment.
Evaluating Crusher Type
Different fine crushers offer different types of crushing actions. For example, impact crushers are ideal for processing materials with low to medium hardness, while cone crushers are more suitable for high-hardness materials. Understanding the application and material type helps in choosing the right crusher type.
Considering Energy Efficiency
Energy efficiency is an important factor when choosing a fine crusher. Selecting a crusher that minimizes power consumption while maintaining high crushing performance reduces operational costs and increases overall productivity.
Operational Flexibility and Ease of Adjustment
Fine crushers that allow for easy adjustments to the crushing gap or settings are preferred, as they provide flexibility in accommodating a range of material types and size requirements. Consider crushers that offer easy setup and adjustment for different material processing needs.
Assessing Maintenance Requirements
The ease of maintenance and the availability of spare parts should also be taken into account. A crusher that requires frequent maintenance or has hard-to-replace parts can increase operational downtime and reduce productivity.
Durability and Wear Resistance
Since fine crushers deal with heavy workloads, choosing a crusher made of durable and wear-resistant materials ensures long-term performance and reduces the frequency of repairs or part replacements.
Reviewing Environmental Considerations
Consideration of environmental factors such as noise levels, dust control, and emissions is also important. Fine crushers that feature advanced dust control and noise reduction technologies help minimize environmental impact and comply with regulations.
Comparing Cost-Effectiveness
While it is important to choose a fine crusher based on performance, the total cost of ownership, including installation, maintenance, and operational costs, should also be factored into the decision-making process to ensure a balance of performance and budget.
Stone Crusher Types
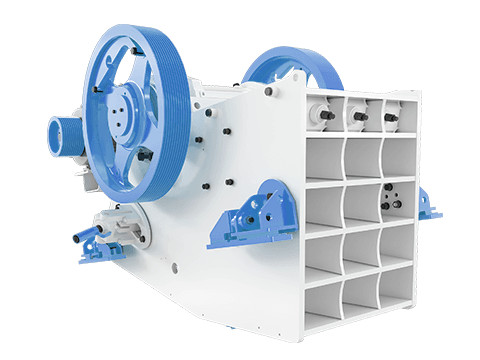
Jaw Crusher
Compressive Crushing: Utilizes compressive force generated by a reciprocating motion between a fixed jaw plate and a movable jaw plate. The material is crushed by progressive compression as it moves downward through the crushing chamber.
Learn more >>
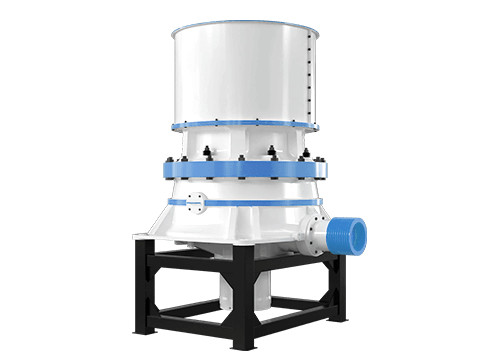
Cone Crusher
Employs interparticle crushing (also called layer compression), where rocks are crushed between a rotating mantle and a concave liner. The eccentric gyratory motion of the mantle creates a compressive force field, inducing fractures along grain boundaries.
Learn more >>
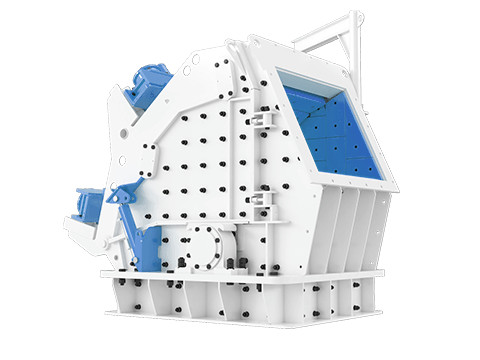
Impact Crusher
Dynamic Impact Crushing: Relies on kinetic energy transfer via high-speed rotors equipped with blow bars or hammers. Material is shattered by direct impact against rotating components or stationary anvils, with secondary fragmentation occurring through particle-on-particle collisions.
Learn more >>
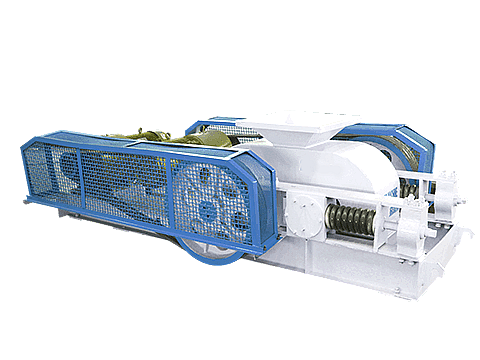
Roll Crusher
Shear-Compression Crushing: Applies shear-compression forces between counter-rotating rolls with textured or smooth surfaces. Material is drawn into the gap (nip angle) and fragmented via tensile failure or surface abrasion.
Learn more >>
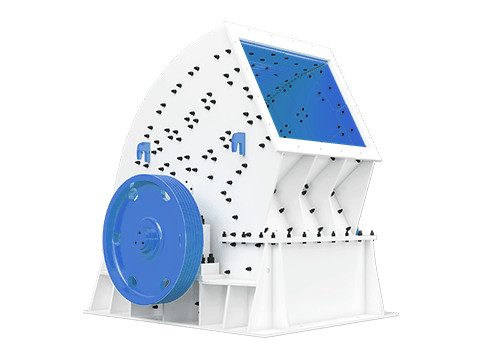
Hammer Crusher
Dynamic Impact with Grinding: Combines high-velocity hammer strikes (rotating hammers on a horizontal shaft) with material grinding against breaker plates or screens. Fragmentation occurs through impact, attrition, and shear.
Learn more >>
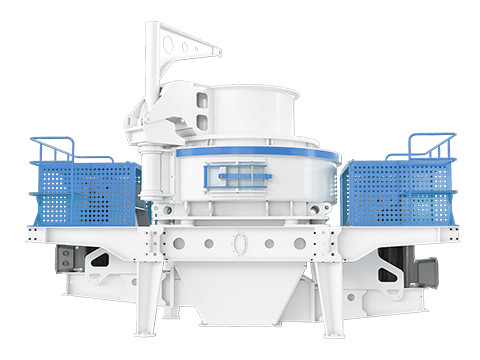
VSI Crusher
Centrifugal Acceleration Crushing: Accelerates material through a high-speed rotor (up to 70 m/s) and projects it against a stationary anvil or rock-lined chamber, exploiting centrifugal force and interparticle collision for fragmentation.
Learn more >>
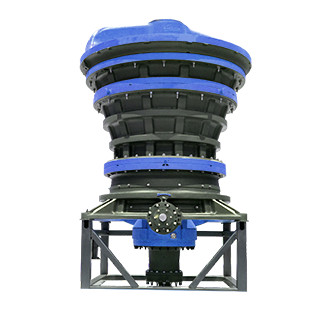
Gyratory Crusher
Conical Compression Crushing: Operates via a conical head gyrating within a concave bowl, generating progressive compression as material moves downward. Combines elements of jaw and cone crushers for ultra-high-capacity primary crushing.
Learn more >>
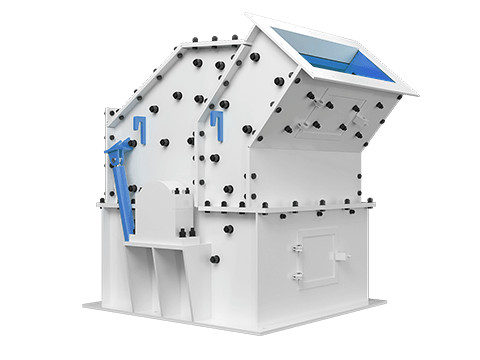
Fine Crusher
Fine Crusher is engineered for reliable and stable operation, making it an ideal choice for fine crushing applications across various industries.
Learn more >>
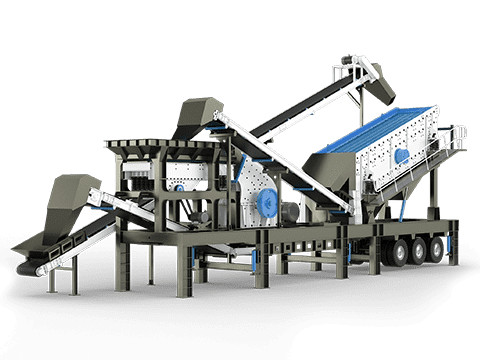
Mobile Crusher
The Mobile Crusher is designed to operate as a primary or secondary unit, making it a versatile choice for various applications.
Learn more >>