Cone Crusher
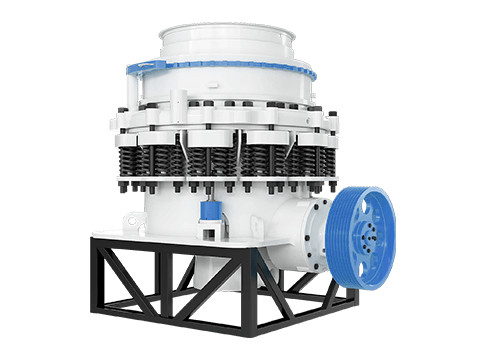
What is Cone Crusher?
Cone crusher is suitable for crushing raw materials in metallurgy, construction, road construction, chemical and silicate industries. According to different crushing principles and different product particle sizes, it is divided into many models. Crusher is widely used in many departments such as mining, smelting, building materials, highways, railways, water conservancy and chemical industries. Cone crusher has large crushing ratio, high efficiency, low energy consumption, uniform product particle size, and is suitable for medium and fine crushing of various ores and rocks.

Working Principle of Cone Crusher
Cone crushers operate through a unique gyrating motion that creates compressive forces to break down materials. At the heart of the machine is an eccentrically rotating mantle that gyrates within a concave bowl liner. As rocks enter the crushing chamber from the top, they are squeezed between the mantle's movement and the stationary concave, causing fractures along natural fault lines in the material. This mechanical advantage allows cone crushers to process hard stones more efficiently than many other crushing methods.
Gyrating Crushing Mechanism
Features an eccentrically rotating mantle that creates powerful compressive forces against the concave bowl liner, efficiently breaking hard materials along natural fault lines.
Multi-Force Reduction
Combines impact, shear, and compression forces for progressive size reduction, producing more uniform aggregates than simple compression crushers.
Hydraulic Adjustment
Modern systems allow on-the-fly adjustments of crusher settings to meet different product requirements without stopping production.
Continuous Output
Delivers steady production of consistently sized aggregates, making it ideal for construction and mining applications requiring uniform material.
The crushing action creates a progressive reduction in material size as particles work their way down through the chamber. Unlike simple compression crushers, cone crushers utilize a combination of impact, shear, and compression forces due to the mantle's gyrating motion. The continuous crushing process ensures a steady output of uniformly sized aggregates, making it ideal for producing consistent material for construction and mining applications. Modern cone crushers often feature hydraulic adjustment systems that allow operators to change the crusher's settings during operation for different product requirements.


Main Components of Cone Crusher
Cone Crusher Types
Maintenance of Cone Crushers
Proper maintenance is essential for ensuring the longevity, efficiency, and reliability of cone crushers. These machines operate under high pressure and heavy loads, making routine inspections and servicing crucial to prevent unexpected breakdowns. Regular maintenance enhances performance, reduces downtime, and lowers operating costs. Understanding key maintenance practices helps operators keep their cone crushers in optimal condition.
Regular Inspection and Monitoring
Frequent visual inspections help detect potential issues before they escalate into major problems. Operators should routinely check for unusual vibrations, excessive noise, and visible signs of wear or damage. Monitoring parameters such as pressure, temperature, and power consumption can provide early warnings of possible malfunctions.
Lubrication System Maintenance
Proper lubrication is critical for reducing friction and preventing overheating of moving parts. Cone crushers require consistent oil flow to keep bearings and bushings in good condition. Regularly checking oil levels, changing oil at recommended intervals, and using high-quality lubricants ensure smooth operation and extend the lifespan of components.
Checking and Replacing Wear Parts
Wear parts such as mantles, concaves, and liners gradually degrade over time due to continuous crushing forces. Regular inspection and timely replacement of these components prevent reduced efficiency and uneven material output. Using high-quality replacement parts enhances durability and minimizes maintenance downtime.
Clearing Material Blockages
Blockages can occur due to oversized feed material, wet conditions, or uneven feeding. Clearing obstructions promptly prevents excessive strain on the crusher and reduces the risk of mechanical failures. Implementing a controlled feeding process minimizes blockages and ensures stable performance.
Hydraulic System Maintenance
The hydraulic system plays a crucial role in adjusting settings and providing overload protection. Regularly inspecting hydraulic lines, checking fluid levels, and ensuring proper valve function help maintain system efficiency. Addressing leaks and replacing worn-out seals prevent pressure loss and system failures.
Checking the Drive System
The drive system, including belts, pulleys, and motors, requires routine maintenance to ensure consistent power transmission. Loose or damaged belts should be adjusted or replaced to maintain proper tension. Checking motor performance and alignment prevents energy losses and mechanical stress on the crusher.
Monitoring the Main Shaft and Bearings
The main shaft and bearings endure high loads during operation, making regular maintenance crucial. Checking for excessive movement, unusual noises, or overheating can help detect bearing wear early. Proper lubrication and timely replacement of worn bearings improve overall machine reliability.
Maintaining the Cooling System
Overheating can lead to performance issues and premature component failure. The cooling system, including fans and heat exchangers, should be inspected regularly to ensure efficient heat dissipation. Cleaning radiator fins and ensuring proper airflow help maintain optimal operating temperatures.
Ensuring Proper Crusher Settings
Adjusting the crusher settings correctly is vital for achieving the desired output size and maximizing efficiency. Operators should routinely check and calibrate settings to maintain consistent performance. Ensuring proper alignment of internal components prevents uneven wear and mechanical strain.
Preventive Maintenance Over Reactive Repairs
Implementing a preventive maintenance schedule reduces the likelihood of costly, unplanned repairs. Routine servicing, timely part replacements, and proactive inspections help avoid sudden breakdowns. A well-maintained cone crusher delivers higher productivity, reduced downtime, and long-term cost savings.
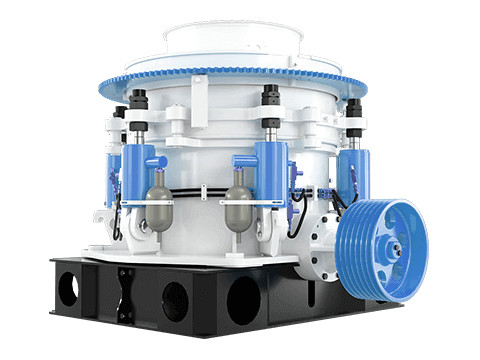
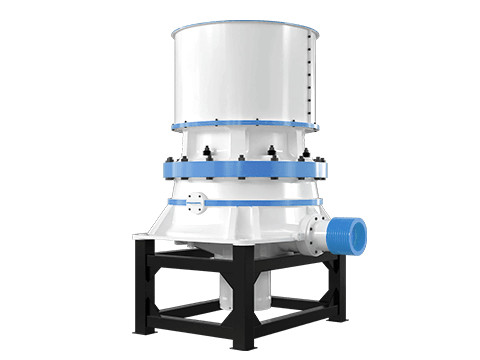
Applications of Cone Crusher
Cone crushers are widely used in various industries due to their ability to deliver efficient crushing performance and produce high-quality aggregates. Their versatility allows them to handle different types of materials and applications, making them an essential tool in mining, construction, and industrial processing. Understanding the key applications of cone crushers highlights their importance in modern material processing operations.
Mining and Mineral Processing
Cone crushers play a crucial role in the mining industry, where they are used to crush hard and abrasive ores. They are commonly utilized in secondary, tertiary, and even quaternary crushing stages to reduce ore size for further processing. Their ability to handle high-pressure crushing makes them ideal for processing materials such as iron ore, copper ore, gold ore, and granite.
Aggregate Production
In the construction industry, cone crushers are essential for producing high-quality aggregates used in concrete, asphalt, and road construction. They ensure uniform particle size and shape, which is vital for the strength and durability of construction materials. By adjusting the crusher settings, operators can produce various aggregate sizes to meet specific project requirements.
Road and Infrastructure Development
Road construction projects require durable and precisely sized aggregates to create stable road surfaces. Cone crushers contribute to this by efficiently breaking down large rocks into smaller, well-graded materials. Their ability to produce consistent aggregates makes them valuable in constructing highways, bridges, and railway foundations.
Recycling and Waste Management
Cone crushers are increasingly used in recycling applications, where they process demolition waste, concrete debris, and asphalt. They help reduce environmental impact by converting waste materials into reusable construction aggregates. This application is crucial in sustainable construction practices and waste reduction efforts.
Metallurgical and Chemical Industries
The metallurgical and chemical industries utilize cone crushers for material processing and size reduction of raw materials used in manufacturing processes. These industries require precise crushing to produce fine powders or specific material sizes for further refining, making cone crushers a valuable asset in their operations.
Sand Production
With the growing demand for manufactured sand, cone crushers are widely used in sand-making plants. They efficiently process raw materials like limestone, basalt, and granite to produce fine sand particles required for construction, plastering, and concrete mixing. Their controlled crushing mechanism ensures minimal waste and optimal particle shape.
Industrial Rock Processing
Various industrial applications require cone crushers to break down large rocks into manageable sizes for use in industrial production. Industries such as glass manufacturing, ceramics, and cement production depend on cone crushers for consistent material output. Their ability to handle different hardness levels makes them ideal for processing a wide range of raw materials.
Enhancing Efficiency in Material Processing
Regardless of the industry, cone crushers contribute to improving efficiency in material processing. Their advanced technology, high crushing capacity, and adaptability to different applications make them indispensable machines. By integrating cone crushers into processing operations, industries can achieve cost-effective and reliable material crushing solutions.
How to Choose the Right Cone Crusher?
Selecting the right cone crusher is essential for achieving efficient material processing and optimal performance in crushing operations. With various models and specifications available, choosing the most suitable cone crusher requires a thorough understanding of material properties, production requirements, and operational considerations. A well-chosen cone crusher ensures higher productivity, reduced downtime, and long-term cost savings. This article explores the key factors to consider when selecting a cone crusher to help industries make informed decisions.
Understanding the Material Characteristics
The first step in choosing a cone crusher is to assess the type of material it will process. Different materials vary in hardness, moisture content, and abrasiveness, which directly affect the performance and wear resistance of the crusher. Hard and abrasive materials, such as granite and basalt, require a cone crusher with robust wear-resistant components, while softer materials, such as limestone, may allow for more flexible options.
Determining the Required Crushing Capacity
Production capacity is a crucial factor in selecting the right cone crusher. It is important to choose a model that can handle the required tonnage per hour without overloading the machine. Overestimating capacity can lead to unnecessary expenses, while underestimating it can cause bottlenecks in production. Evaluating both peak and average production needs helps in selecting a crusher that ensures consistent and efficient output.
Considering the Feed and Output Size
The size of the feed material and the desired output size play a significant role in determining the appropriate cone crusher. A crusher with a larger feed opening is suitable for handling bigger rocks, while a well-designed chamber and adjustable settings allow for precise control of the final product size. Ensuring the right match between feed and discharge sizes helps optimize efficiency and minimize energy consumption.
Evaluating Crushing Stages and Circuit Design
Different crushing applications require varying stages of crushing. Cone crushers are commonly used in secondary, tertiary, and even quaternary crushing stages. Understanding where the crusher fits into the overall circuit—whether it follows a primary jaw crusher or is part of a multi-stage process—helps in selecting the right model with the necessary features for optimal performance.
Energy Efficiency and Power Requirements
Energy consumption is a major consideration when choosing a cone crusher. Selecting a crusher with an efficient power system can significantly reduce operational costs while maintaining high productivity. Modern cone crushers often come with advanced technologies such as hydraulic systems and automation, which help improve energy efficiency and ease of operation.
Assessing Durability and Maintenance Needs
A cone crusher's durability directly affects its operational lifespan and overall cost-effectiveness. Crushers made with high-quality materials and reinforced components offer longer wear life and require less frequent maintenance. Additionally, models with easy-to-access wear parts and user-friendly maintenance features help minimize downtime and improve overall efficiency.
Comparing Different Cone Crusher Models
Manufacturers offer a variety of cone crusher models, each designed for specific applications. Comparing specifications such as crushing chamber design, liner options, and automation features helps in selecting the most suitable machine. Some advanced models come with real-time monitoring systems and hydraulic adjustment capabilities, providing greater flexibility and ease of use.
Choosing a Reliable Manufacturer and Supplier
Partnering with a reputable manufacturer or supplier is essential when purchasing a cone crusher. A well-established company provides high-quality equipment, reliable after-sales support, and warranties. Working with a trusted supplier ensures access to genuine spare parts, technical assistance, and long-term service reliability.
Making the Right Investment
Selecting the right cone crusher requires balancing performance, durability, efficiency, and cost considerations. Conducting a thorough assessment of material requirements, production needs, and available technologies helps in making an informed decision. By choosing a well-suited cone crusher, industries can optimize crushing operations, reduce operational costs, and achieve long-term productivity.
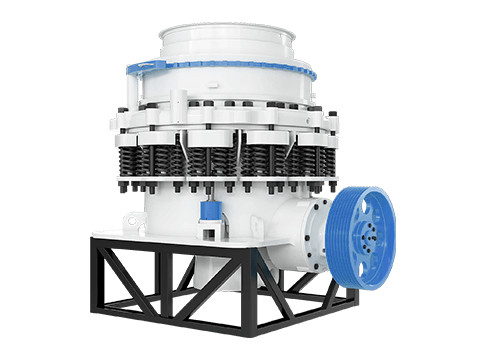
Specifications
HP-Type
Model | Cavity Type | Feeding Opening(mm) | Closed Side Feeding Opening(mm) | Minimum Discharge Opening(mm) | Motor Power(kW) | Capacity(t/h) |
---|---|---|---|---|---|---|
HP100 | C1 Extra coarse | 175 | 140 | 19 | 4P 100 | 45 - 145 |
C2 Coarse | 125 | 105 | 13 | |||
M Medium | 100 | 70 | 10 | |||
F1 Fine | 71 | 50 | 9 | |||
F2 Extra fine | 33 | 20 | 6 | |||
HP200 | C1 Extra coarse | 235 | 190 | 19 | 4P 160 | 90 - 250 |
C2 Coarse | 171 | 120 | 16 | |||
M Medium | 150 | 95 | 13 | |||
F1 Fine | 116 | 70 | 8 | |||
F2 Extra fine | 116 | 70 | 8 | |||
HP300 | C1 Extra coarse | 265 | 230 | 25 | 4P 220 | 115 - 440 |
C2 Coarse | 240 | 210 | 20 | |||
M Medium | 190 | 150 | 15 | |||
F1 Fine | 145 | 105 | 11 | |||
F2 Extra fine | 120 | 80 | 8 | |||
HP400 | C1 Extra coarse | 360 | 290 | 30 | 4P 315 | 140 - 630 |
C2 Coarse | 310 | 250 | 25 | |||
M Medium | 260 | 196 | 20 | |||
F1 Fine | 182 | 110 | 13 | |||
F2 Extra fine | 155 | 90 | 10 | |||
HP500 | C1 Extra coarse | 370 | 330 | 38 | 4P 400 | 175 - 790 |
C2 Coarse | 320 | 280 | 28 | |||
M Medium | 245 | 210 | 22 | |||
F1 Fine | 180 | 130 | 13 | |||
F2 Extra fine | 150 | 110 | 10 | |||
HP800 | C1 Extra coarse | 450 | 352 | 38 | 4P 830 | 260 - 1200 |
C2 Coarse | 373 | 298 | 32 | |||
M Medium | 340 | 275 | 25 | |||
F1 Fine | 280 | 230 | 16 | |||
F2 Extra fine | 235 | 150 | 10 |
S-Type
Model | Cavity Type | Maximum Feed Inlet Size (mm) | Minimum Discharge Opening (mm) | Capacity (t/h) | Maximum Installed Power (kW) |
---|---|---|---|---|---|
SH420 | S1 (Extra coarse) | 240 | 22 | 85 - 170 | 90 |
S2 (Medium coarse) | 200 | 19 | 70 - 130 | ||
SH420 | H1 (Fine) | 135 | 10 | 45 - 130 | |
H2 (Medium fine) | 65 | 8 | 35 - 80 | ||
H3 (Extra fine) | 38 | 4 | 27 - 60 | ||
SH430 | S1 (Extra coarse) | 360 | 25 | 120 - 345 | 160 |
S2 (Medium coarse) | 300 | 22 | 105 - 305 | ||
S3 (Coarse) | 235 | 19 | 90 - 275 | ||
SH430 | H1 (Fine) | 185 | 13 | 60 - 210 | |
H2 (Medium fine) | 90 | 10 | 65 - 165 | ||
H3 (Extra fine) | 50 | 6 | 48 - 105 | ||
SH440 | S1 (Extra coarse) | 450 | 35 | 255 - 605 | 250 |
S2 (Medium coarse) | 400 | 29 | 215 - 515 | ||
S3 (Coarse) | 300 | 25 | 190 - 490 | ||
SH440 | H1 (Fine) | 215 | 16 | 110 - 395 | |
H2 (Medium fine) | 110 | 13 | 115 - 340 | ||
H3 (Extra fine) | 70 | 8 | 90 - 225 | ||
SH660 | S1 (Extra coarse) | 560 | 41 | 355 - 1050 | 315 |
S2 (Medium coarse) | 500 | 38 | 305 - 895 | ||
SH660 | H1 (Fine) | 275 | 16 | 170 - 665 | |
H2 (Medium fine) | 135 | 16 | 190 - 505 | ||
H3 (Extra coarse) | 65 | 13 | 205 - 320 |
Related Articles
Comprehensive Guide to Gear Wear Detection for Cone Crushers: 2025 Standardized Testing Procedures
In-Depth Analysis of Cone Crusher Bearing Lubrication Systems: 2025 Best Practices Guide
The Application of Cone Crushers in Construction Waste Recycling
The Application of Cone Crushers in Copper Mining and Processing
A Guide to Selecting Small Cone Crushers for Aggregate Production
Understanding Iron Ore Crushing: A Comprehensive Guide to Crusher Requirements and Selection
Stone Crusher Types
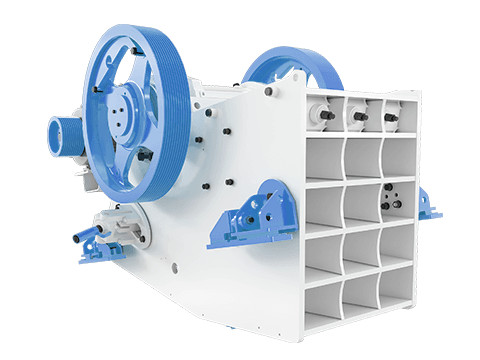
Jaw Crusher
Compressive Crushing: Utilizes compressive force generated by a reciprocating motion between a fixed jaw plate and a movable jaw plate. The material is crushed by progressive compression as it moves downward through the crushing chamber.
Primary Crushing High Reduction Ratio
Learn more >>
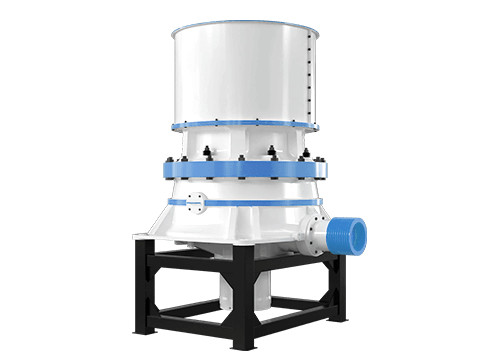
Cone Crusher
Employs interparticle crushing (also called layer compression), where rocks are crushed between a rotating mantle and a concave liner. The eccentric gyratory motion of the mantle creates a compressive force field, inducing fractures along grain boundaries.
Secondary Crushing Hydraulic Adjustment
Learn more >>
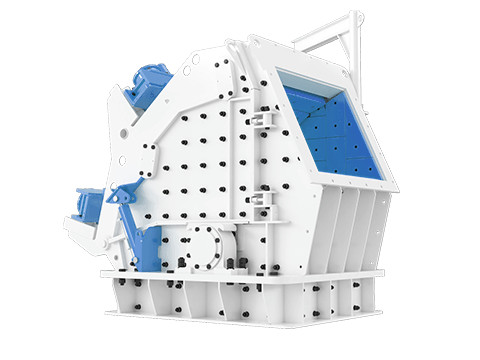
Impact Crusher
Dynamic Impact Crushing: Relies on kinetic energy transfer via high-speed rotors equipped with blow bars or hammers. Material is shattered by direct impact against rotating components or stationary anvils, with fragmentation occurring through particle-on-particle collisions.
High-Speed Impact Cubical Aggregate
Learn more >>
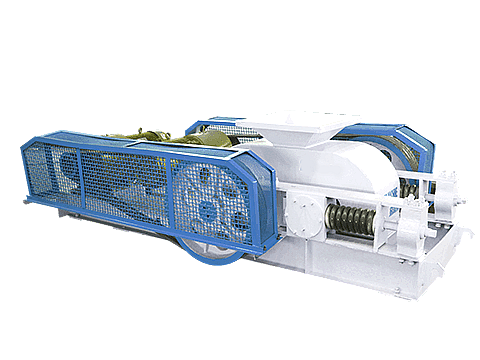
Roll Crusher
Shear-Compression Crushing: Applies shear-compression forces between counter-rotating rolls with textured or smooth surfaces. Material is drawn into the gap (nip angle) and fragmented via tensile failure or surface abrasion.
Double Roll Design Low Fines Production
Learn more >>
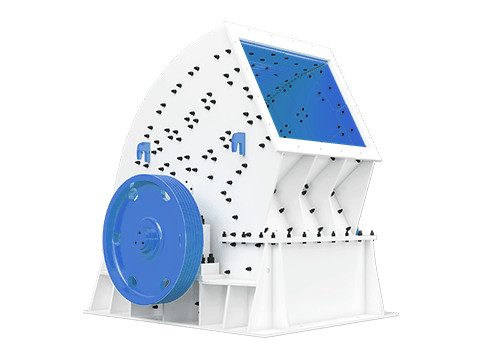
Hammer Crusher
Dynamic Impact with Grinding: Combines high-velocity hammer strikes (rotating hammers on a horizontal shaft) with material grinding against breaker plates or screens. Fragmentation occurs through impact, attrition, and shear.
High-Speed Hammer Brittle Material Crushing
Learn more >>
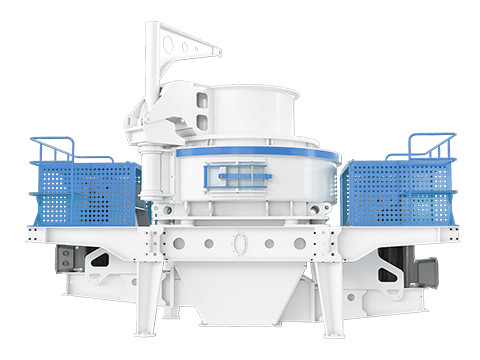
VSI Crusher
Centrifugal Acceleration Crushing: Accelerates material through a high-speed rotor (up to 70 m/s) and projects it against a stationary anvil or rock-lined chamber, exploiting centrifugal force and interparticle collision for fragmentation.
Vertical Shaft Impact Cubical Product Shape
Learn more >>
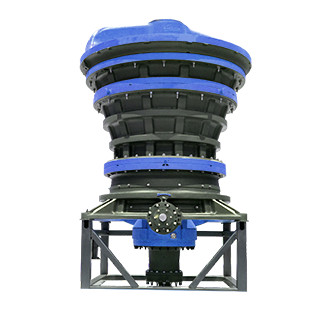
Gyratory Crusher
Conical Compression Crushing: Operates via a conical head gyrating within a concave bowl, generating progressive compression as material moves downward. Combines elements of jaw and cone crushers for ultra-high-capacity primary crushing.
Primary Crushing High Capacity
Learn more >>
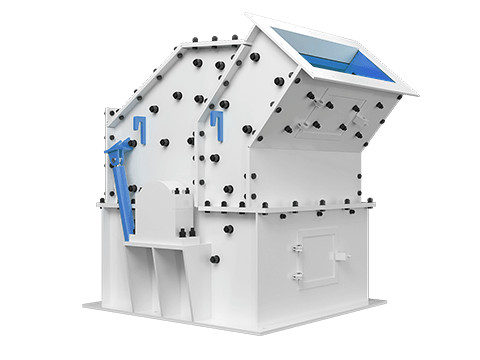
Fine Crusher
With a simplified structure and convenient maintenance, Fine Crusher delivers high production capacity and a long service life for its hammer heads. It is widely used for crushing granite, basalt, limestone, river pebbles, cement clinker, quartz stone, iron ore, bauxite, and more.
Precision Crushing Ultra-Fine Output
Learn more >>
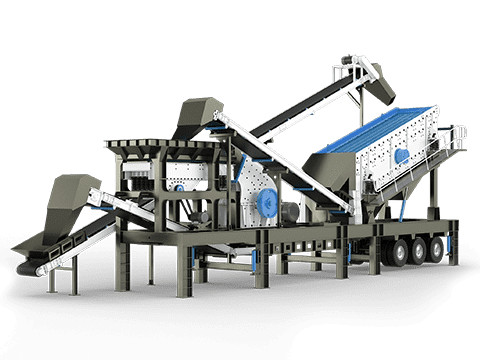
Mobile Crusher
Mobile crushers are advanced crushing machines designed for on-site material processing, offering high mobility and flexibility. They can be easily transported between job sites, making them ideal for construction, mining, and recycling applications.
On-Site Crushing Track / Wheel Mobility
Learn more >>