Types of Crusher Machines
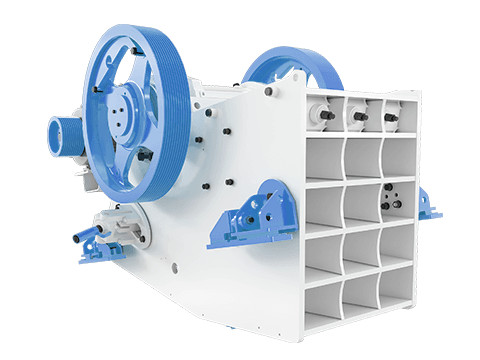
Jaw Crusher
Compressive Crushing: Utilizes compressive force generated by a reciprocating motion between a fixed jaw plate and a movable jaw plate. The material is crushed by progressive compression as it moves downward through the crushing chamber.
Learn more >>
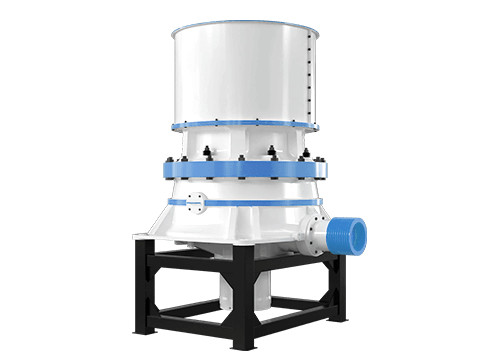
Cone Crusher
Employs interparticle crushing (also called layer compression), where rocks are crushed between a rotating mantle and a concave liner. The eccentric gyratory motion of the mantle creates a compressive force field, inducing fractures along grain boundaries.
Learn more >>
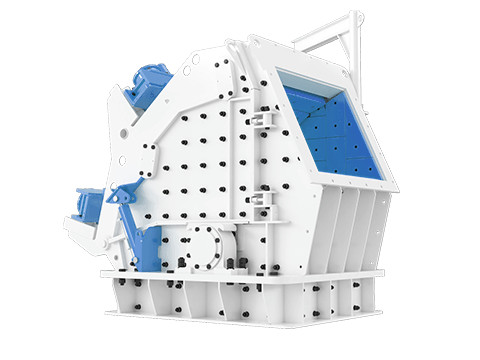
Impact Crusher
Dynamic Impact Crushing: Relies on kinetic energy transfer via high-speed rotors equipped with blow bars or hammers. Material is shattered by direct impact against rotating components or stationary anvils, with secondary fragmentation occurring through particle-on-particle collisions.
Learn more >>
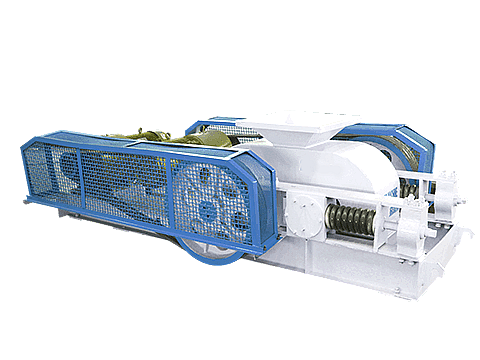
Roll Crusher
Shear-Compression Crushing: Applies shear-compression forces between counter-rotating rolls with textured or smooth surfaces. Material is drawn into the gap (nip angle) and fragmented via tensile failure or surface abrasion.
Learn more >>
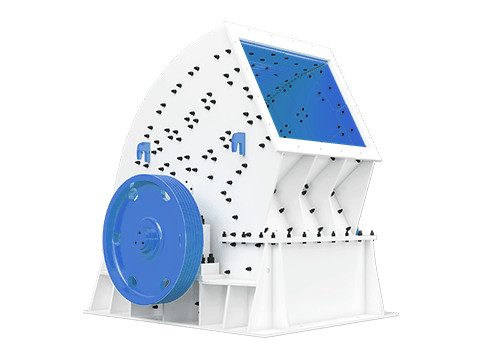
Hammer Crusher
Dynamic Impact with Grinding: Combines high-velocity hammer strikes (rotating hammers on a horizontal shaft) with material grinding against breaker plates or screens. Fragmentation occurs through impact, attrition, and shear.
Learn more >>
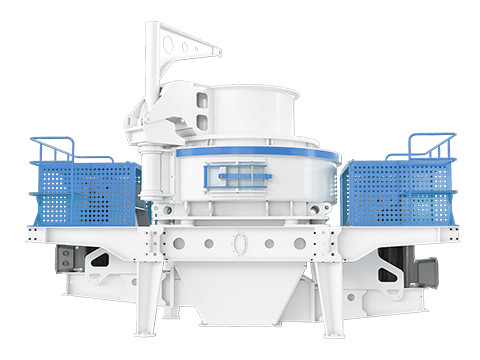
VSI Crusher
Centrifugal Acceleration Crushing: Accelerates material through a high-speed rotor (up to 70 m/s) and projects it against a stationary anvil or rock-lined chamber, exploiting centrifugal force and interparticle collision for fragmentation.
Learn more >>
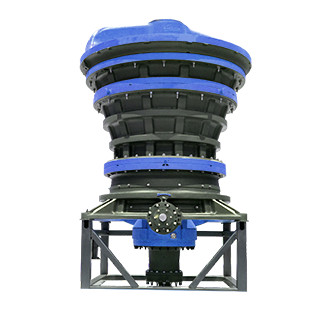
Gyratory Crusher
Conical Compression Crushing: Operates via a conical head gyrating within a concave bowl, generating progressive compression as material moves downward. Combines elements of jaw and cone crushers for ultra-high-capacity primary crushing.
Learn more >>
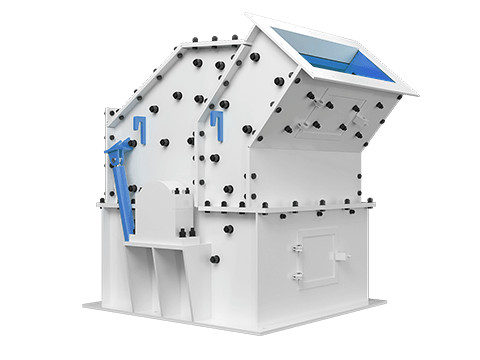
Fine Crusher
Fine Crusher is engineered for reliable and stable operation, making it an ideal choice for fine crushing applications across various industries.
Learn more >>
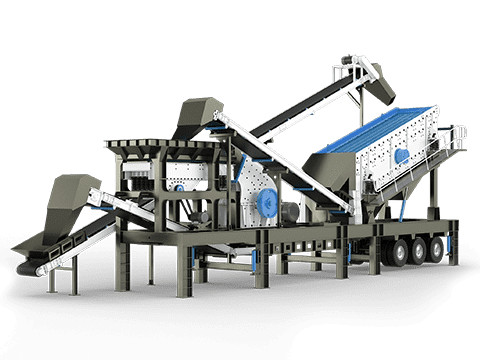
Mobile Crusher
The Mobile Crusher is designed to operate as a primary or secondary unit, making it a versatile choice for various applications.
Learn more >>
What Are Crusher Machines?
Definition of Crusher Machine
Crushers are machines designed to break large materials into smaller, more manageable pieces. They play a crucial role in various industries such as mining, construction, and recycling by reducing the size of raw materials, facilitating their further processing. Crushers can handle a variety of materials, including rock, stone, coal, and recycling debris, turning them into products that can be used in various applications. In essence, crushers help in material processing by breaking down large, hard-to-handle chunks of material into smaller pieces that are easier to transport, handle, and process further in the production cycle.
Types of Crushers and Their Functions
There are several types of crushers, each designed to handle specific materials and applications. The most common types include:
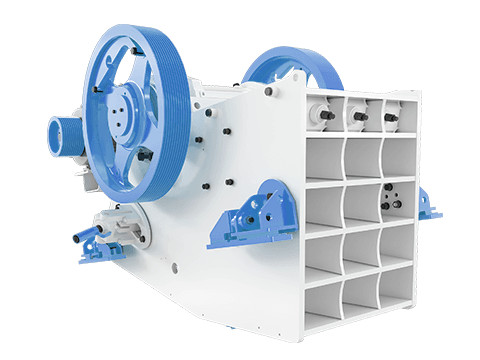
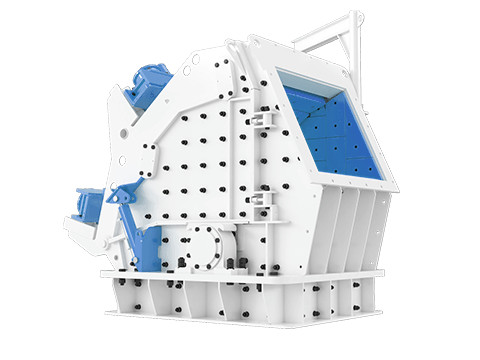
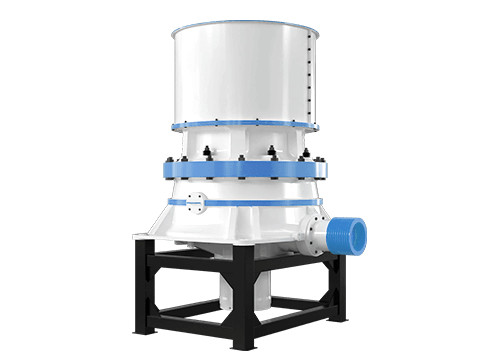
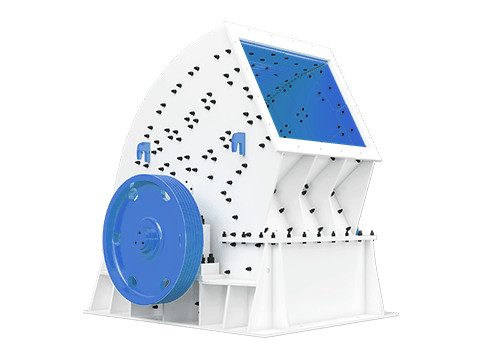
Jaw Crushers – These are primarily used for primary crushing. They work by compressing the material between two jaws, one of which is stationary and the other is movable. Jaw crushers are ideal for breaking down large, hard materials such as rocks and concrete.
Impact Crushers – These crushers use high-speed impact forces to break down materials. They are suitable for secondary and tertiary crushing and are often used for softer materials such as limestone and sandstone. Impact crushers are particularly useful when producing high-quality aggregates.
Cone Crushers – Cone crushers are used for secondary and tertiary crushing. They work by squeezing the material between a rotating cone and a stationary cone, making them effective for reducing the size of hard, abrasive materials. They are ideal for processing ores and aggregates in industries such as mining and construction.
Hammer Crushers – These crushers use rotating hammers to crush materials. They are typically used for soft to medium-hard materials like coal, gypsum, or limestone. Hammer crushers are often used in situations where a high reduction ratio is required and are effective in producing fine products.
Importance of Crushers in Material Processing
Crushers are essential in material processing as they convert large, bulky raw materials into smaller, usable sizes that are better suited for further processing. In mining, crushers break down large ore samples into smaller fragments, making it easier to extract valuable minerals. In construction and demolition, crushers reduce materials like concrete, asphalt, and stone into manageable pieces for recycling or reuse. In recycling, crushers allow for the recovery of valuable materials from waste products, such as metals, plastics, and concrete, contributing to environmental sustainability. Overall, crushers enable a smoother, more efficient material handling process, helping industries achieve higher productivity and lower costs.
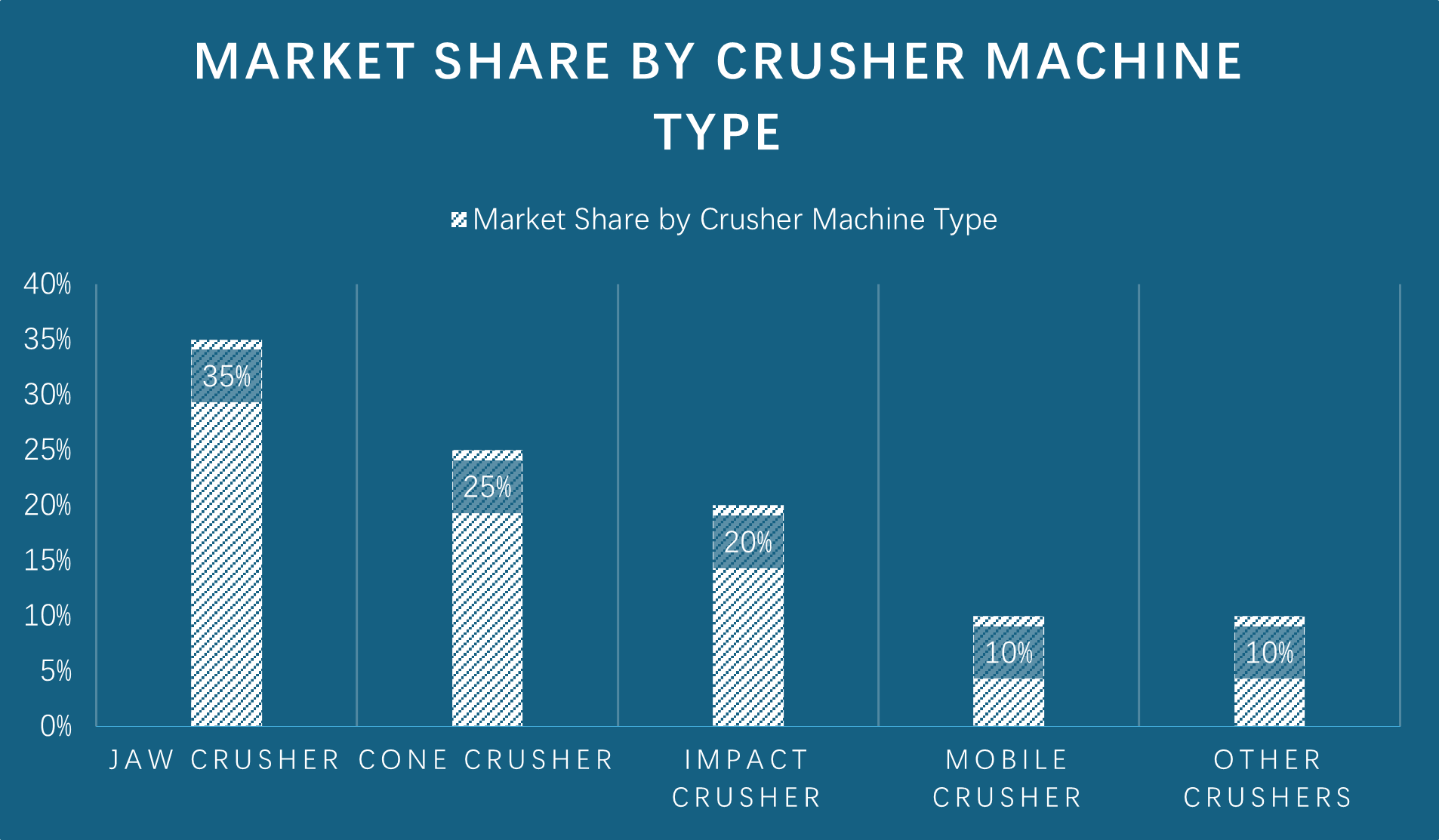
How Do Crushers Improve Material Processing?
Primary Crushing: Breaking Large Materials
Crusher machines play a crucial role in the initial stage of material processing by breaking down large raw materials into smaller, more manageable pieces. In industries such as mining, quarrying, and construction, primary crushers handle oversized materials like rocks, ores, and demolition debris. Jaw crushers and gyratory crushers are commonly used in this stage, as they apply high pressure to crush hard and abrasive materials. By reducing the material size at the outset, primary crushing makes transportation and further processing easier and more efficient.
Secondary and Tertiary Crushing: Fine Tuning for Specific Applications
Once the material has been reduced to a manageable size, secondary and tertiary crushers refine it further to meet specific application needs. Cone crushers, impact crushers, and hammer crushers are commonly used in these stages to produce finer aggregates, sand, or mineral concentrates. Secondary and tertiary crushing allows for precise control over particle size distribution, ensuring that the final product meets industry standards for use in construction, asphalt production, or other applications.
Improved Material Flow and Homogenization
Efficient crushing enhances material flow by creating uniform particle sizes, which leads to improved handling and processing downstream. In industries like cement production and aggregate processing, consistent material sizes improve mixing efficiency and ensure high-quality final products. Crushers help homogenize materials, preventing inconsistencies that could affect the structural integrity of buildings, roads, or other infrastructure projects.
Reduction of Waste and Maximization of Yield
Modern crushers are designed to minimize waste and maximize yield by optimizing crushing efficiency. By breaking down materials into usable sizes with minimal fine dust or unusable fragments, crushers help reduce raw material wastage. Additionally, recycling crushers process construction and demolition waste, transforming old concrete, asphalt, and bricks into reusable aggregates. This not only conserves natural resources but also reduces disposal costs, supporting sustainable material management practices.
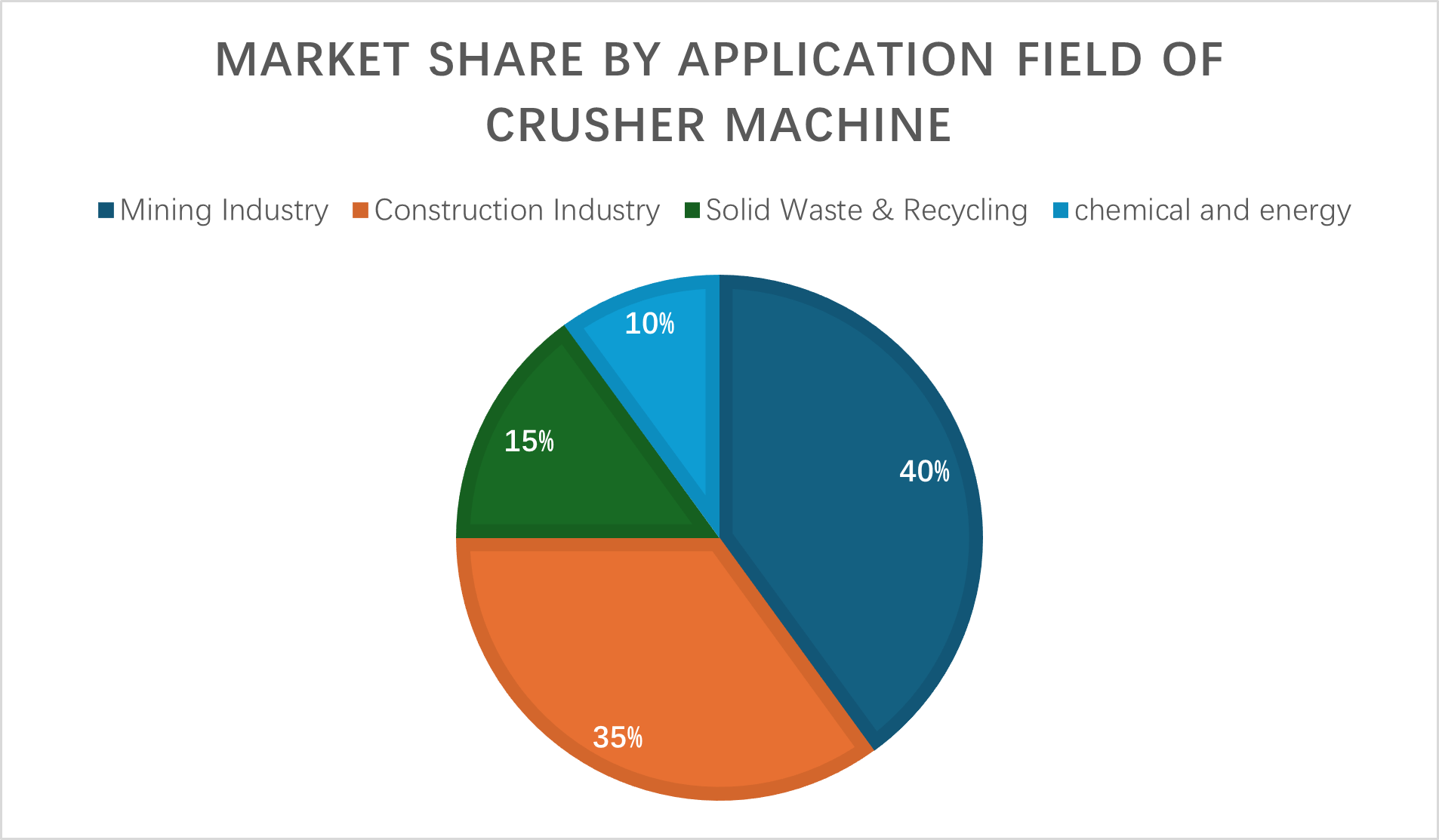
How Crusher Machines Improve Profitability for Your Business
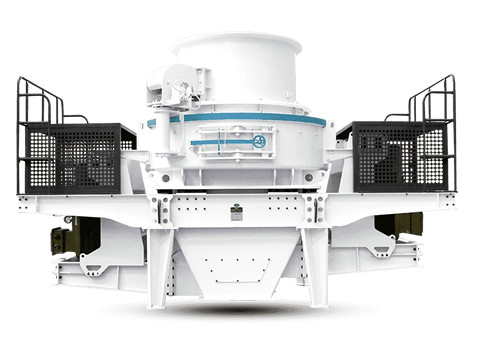
Lower Operating Costs
Investing in high-efficiency crusher machines can significantly reduce operating costs for businesses involved in material processing. Modern crushers are designed with energy-efficient technologies that minimize power consumption while maintaining high performance. Additionally, advanced wear-resistant components and automated maintenance systems help reduce downtime and maintenance expenses. By optimizing fuel and electricity usage, businesses can cut production costs while improving overall profitability.
Increased Throughput and Output
Optimized crusher performance translates to increased processing capacity and higher output. Advanced crushing machines utilize innovative designs, such as variable speed settings and automated adjustment systems, to maximize throughput. Whether in mining, quarrying, or construction, a well-configured crushing system ensures that materials are processed faster and more efficiently, reducing bottlenecks and enhancing production rates. This increased efficiency allows businesses to meet growing market demands without requiring additional equipment investments.
Maximizing Product Quality and Consistency
Crushers play a vital role in delivering high-quality and consistent end products. By precisely controlling particle size, shape, and composition, modern crushers ensure that processed materials meet industry standards. Consistent product quality improves the reliability of raw materials for downstream applications, such as concrete production, asphalt manufacturing, and road construction. This not only enhances customer satisfaction but also strengthens a company’s reputation for delivering superior materials.