Impact Crusher
Impact crusher, is mainly used for processing materials that often need to be moved in metallurgy, chemical industry, building materials, hydropower and other industries. It is especially used for operations with mobile stones such as highways, railways, and hydropower projects. It can adopt a variety of configurations according to the type of raw materials, scale and requirements of finished materials.
Working principle
The impact crusher uses the high-speed rotation of the hammer on the rotor to hit the material onto the impact plate, and uses the impact force to crush the material.
Main functions
Suitable for medium-hard materials (such as concrete blocks and asphalt), producing aggregates with uniform particle shape.
Purpose
Further refine the materials after preliminary crushing to improve the availability of materials.
Main Components of Impact Crusher
Impact Crusher Types
Maintenance of Impact Crushers
Proper maintenance of impact crushers is essential to ensure their longevity, efficiency, and safety. Regular maintenance not only reduces the risk of unexpected breakdowns but also improves performance, lowers operational costs, and extends the service life of the equipment. The maintenance procedures typically focus on key components such as the rotor, blow bars, impact plates, and bearings, among others.
Routine Inspections
Routine inspections of critical parts such as the rotor, blow bars, and impact plates are necessary to detect early signs of wear or damage. By identifying potential issues early, operators can prevent more significant damage and costly repairs. Regular visual inspections, along with checks for cracks, deformations, or excessive wear, are crucial for maintaining operational efficiency.
Impact crushers are often subject to material blockages due to the accumulation of debris or oversized rocks. Regular inspection of the feed port, discharge chute, and other areas prone to blockages can help avoid downtime and ensure smooth material flow through the crusher.
Lubrication and Cooling
Proper lubrication of the crusher’s moving parts, including bearings and the rotor, is crucial to minimize friction and wear. Routine oil or grease replacement, along with checking for leaks, ensures the parts continue to function smoothly. A well-lubricated crusher operates at optimal efficiency and has a longer lifespan.
Increased heat during operation can affect the performance of the impact crusher and lead to overheating of the components. Regularly checking and maintaining the cooling system, including the radiators and oil coolers, is essential for preventing overheating and ensuring that the machine operates under ideal conditions.
Wear Parts Maintenance
The blow bars are among the most heavily worn parts in an impact crusher, as they directly interact with the material being crushed. Regular inspection for wear and tear is vital. When the blow bars become excessively worn, they should be replaced promptly to maintain the crusher’s efficiency and reduce the risk of damage to other components.
Impact plates are also subject to wear from constant material impact. Inspecting these components for cracks, deformations, or severe wear helps maintain consistent crushing performance. Worn impact plates should be replaced or repaired to ensure the machine continues to operate efficiently.
Adjusting and Tightening Components
The discharge opening of the impact crusher needs to be adjusted based on the desired output size. Over time, these adjustments may become less effective due to wear on the adjustment mechanisms. Periodic checks and adjustments ensure that the crusher maintains the desired particle size distribution and production capacity.
Impact crushers contain many bolts and fasteners that can loosen over time due to vibrations during operation. Regularly checking and tightening bolts, nuts, and fasteners can prevent operational issues and avoid potential safety hazards.
Cleaning and Debris Removal
Accumulation of dust, debris, and material residues can affect the performance of the impact crusher. Regular cleaning of external surfaces, feed ports, and discharge areas prevents material buildup, reduces wear on components, and ensures smooth operation.
Regular cleaning of the feed hopper and discharge conveyor is essential to prevent clogging and material flow issues. Ensuring that these areas remain clear of obstructions helps the crusher maintain optimal throughput and reduces the risk of system overloads.
Monitoring and Adjusting Operating Parameters
Monitoring and adjusting the rotational speed of the rotor and the feed rate are essential to optimizing crusher performance. Running the crusher at the correct settings ensures that it operates at peak efficiency while preventing overloading or excessive wear on components.
Unusual vibrations or noise can indicate potential problems with the crusher, such as misalignment, imbalance, or internal wear. Regular monitoring of vibration and noise levels allows for early detection of issues and prevents more serious damage from occurring.
General Maintenance Practices
Safety should always be a top priority during maintenance procedures. Properly locking out the machine and following standard operating procedures ensures that maintenance work is carried out safely. Using protective gear and following manufacturer guidelines can help prevent accidents and injuries.
Maintaining a log of inspections, repairs, and replacements helps track the condition of the crusher over time. Keeping detailed records enables better forecasting for future maintenance needs and helps identify recurring issues that may require more significant repairs or component upgrades.
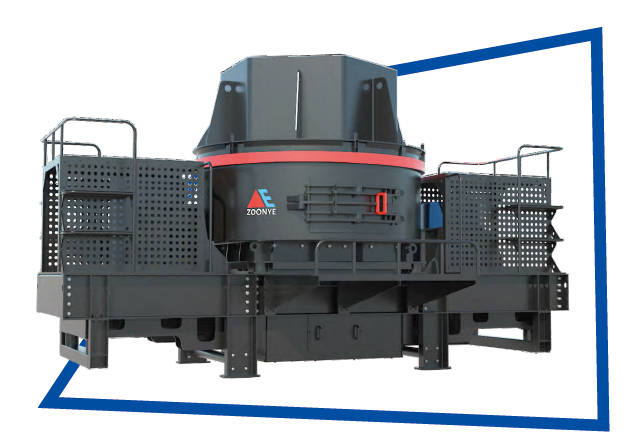
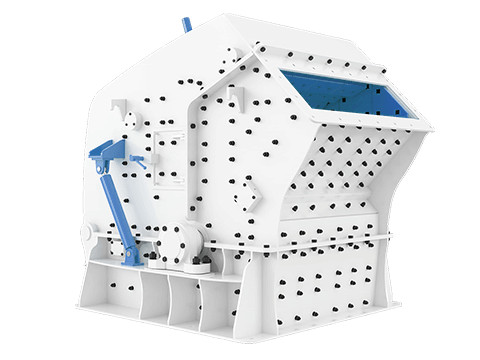
Applications of Impact
Impact crushers are widely used in various industries due to their versatile and efficient crushing capabilities. These crushers work by utilizing impact force to break down materials, making them ideal for processing soft to medium-hard materials in mining, construction, and recycling operations. Their unique ability to produce different particle sizes and shapes makes them an essential tool for producing high-quality aggregates, recycled materials, and other crushed products.
Crushing of Construction and Demolition Waste
One of the most important applications of impact crushers is in the recycling of construction and demolition (C&D) waste. Impact crushers efficiently process materials such as concrete, asphalt, and brick, reducing them to smaller, reusable pieces. This is especially useful for producing recycled aggregates that can be used in road construction, building materials, and other applications.
By processing construction and demolition waste, impact crushers help reduce the amount of material that ends up in landfills. This contributes to sustainable practices in the construction industry and supports the circular economy by enabling the reuse of materials in new projects.
Mining and Quarrying Applications
In mining and quarrying operations, impact crushers are employed to break down harder rocks and materials like limestone, gypsum, and gravel. Their ability to handle abrasive materials while producing uniform particle sizes makes them ideal for use in the extraction of aggregates and minerals.
Impact crushers are highly effective in producing fine aggregates for use in concrete and asphalt production. They ensure consistent gradation and particle shape, making the crushed material ideal for applications where high-quality aggregates are required.
Manufactured Sand Production
Impact crushers are commonly used in the production of manufactured sand, a key component in concrete mixtures. These crushers can produce fine, uniform sand that meets the stringent quality requirements for construction, ensuring better performance and durability in concrete applications.
With the increasing demand for natural sand and the depletion of many sand sources, impact crushers offer an excellent alternative for producing manufactured sand. By crushing materials like granite, limestone, or basalt, they generate sand that is suitable for construction purposes while reducing dependency on natural sand sources.
Recycling Applications
Impact crushers are used in recycling operations to break down materials like glass, metals, and plastics. Their ability to produce consistent and fine material sizes makes them ideal for recycling operations where processed material can be reused in various industries, including packaging, manufacturing, and construction.
Glass recycling plants often use impact crushers to break down glass bottles and containers into smaller, reusable pieces. Similarly, metal scrap processing facilities utilize impact crushers to reduce the size of scrap metal before it is sent for further processing, such as smelting or refining.
Agricultural and Industrial Applications
In agriculture, impact crushers are used to break down organic materials such as wood, biomass, and agricultural waste. These materials are often processed into biofuels, animal bedding, or compost, contributing to sustainable agricultural practices.
Impact crushers also play a significant role in the processing of industrial waste materials. They break down scrap and other industrial by-products, turning them into useful materials for recycling or repurposing in other industries, helping to reduce waste and minimize environmental impact.
Other Construction Applications
Impact crushers are often used in the production of road base materials. By crushing large aggregates into smaller sizes, they create materials that meet specifications for use in base layers of roads and other infrastructure projects. The high-quality crushed material produced by impact crushers ensures the stability and durability of roadways.
Impact crushers are also employed in landscaping projects to produce decorative aggregates, gravel, and other materials used for pathways, driveways, and other surface treatments. Their ability to produce consistent particle shapes and sizes makes them ideal for these aesthetic applications.
How to Choose the Right Impact Crusher?
Choosing the right impact crusher is essential for achieving efficient material processing, reducing operational costs, and ensuring high-quality output. With various models and configurations available, selecting the most suitable impact crusher requires careful evaluation of material characteristics, production requirements, and operational conditions. A well-chosen impact crusher can enhance productivity, minimize downtime, and improve overall profitability. This article explores the key factors to consider when selecting an impact crusher for your specific needs.
Understanding Material Characteristics
The type and properties of the material to be processed play a crucial role in determining the right impact crusher. Materials with different hardness, abrasiveness, and moisture content require specific crusher configurations. Soft to medium-hard materials, such as limestone, concrete, and gypsum, are well-suited for impact crushers, while harder and more abrasive materials may require specialized wear-resistant components.
Evaluating Crushing Capacity and Production Needs
The required production capacity is an important factor when selecting an impact crusher. The crusher must be capable of handling the required tonnage per hour while maintaining efficiency and consistent output. Choosing a model with the right balance of power, rotor speed, and feed size ensures that production goals are met without overloading the machine.
Considering Feed Size and Final Product Requirements
The size of the input material and the desired output size determine the appropriate impact crusher configuration. A larger feed opening allows the crusher to process bigger chunks of material, reducing the need for pre-crushing. Additionally, adjustable settings enable precise control over the final product size, ensuring that the crusher meets specific project requirements.
Assessing Rotor Design and Impact Force
The rotor is the core component of an impact crusher, responsible for delivering the necessary crushing force. Different rotor designs and configurations influence the efficiency and performance of the crusher. A high-speed rotor generates greater impact force, improving material reduction and shaping, while adjustable blow bars and liner configurations enhance versatility in various applications.
Energy Efficiency and Power Consumption
Energy efficiency is a key consideration when selecting an impact crusher. Models with advanced power-saving features, such as variable-speed drives and intelligent control systems, help reduce energy consumption while maintaining high productivity. Opting for an energy-efficient crusher can significantly lower operational costs and improve environmental sustainability.
Durability and Maintenance Considerations
A durable impact crusher with wear-resistant components ensures long-term reliability and reduced maintenance costs. Features such as replaceable wear liners, easy-access maintenance points, and hydraulic adjustment systems simplify upkeep and minimize downtime. Selecting a crusher with user-friendly maintenance features improves operational efficiency and extends equipment lifespan.
Comparing Different Impact Crusher Models
Manufacturers offer a wide range of impact crushers, each designed for specific applications. Comparing factors such as rotor speed, chamber design, automation features, and adjustability helps in selecting the best model. Some advanced impact crushers come equipped with real-time monitoring systems that optimize performance and detect potential issues before they cause disruptions.
Choosing a Reliable Manufacturer and Supplier
Partnering with a reputable manufacturer or supplier is essential when investing in an impact crusher. Established manufacturers provide high-quality equipment, reliable technical support, and access to genuine spare parts. Working with a trusted supplier ensures long-term operational efficiency and reduces the risk of unexpected downtime.
Making an Informed Decision
Selecting the right impact crusher requires a thorough evaluation of material requirements, production goals, and operational efficiency. By considering factors such as feed size, crushing capacity, rotor design, and maintenance needs, businesses can choose an impact crusher that optimizes productivity and cost-effectiveness. A well-chosen crusher enhances material processing efficiency and ensures consistent, high-quality output for various industrial applications.
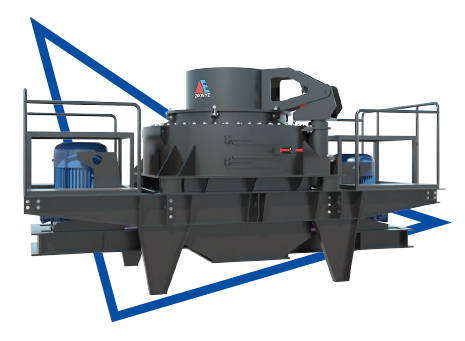
Stone Crusher Types
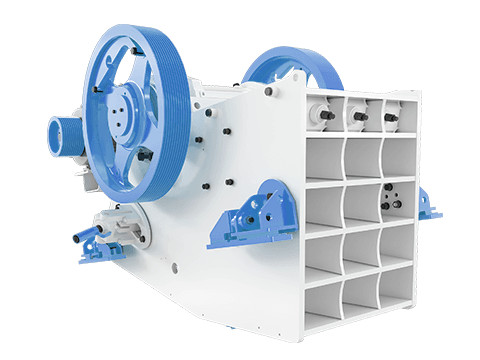
Jaw Crusher
Compressive Crushing: Utilizes compressive force generated by a reciprocating motion between a fixed jaw plate and a movable jaw plate. The material is crushed by progressive compression as it moves downward through the crushing chamber.
Learn more >>
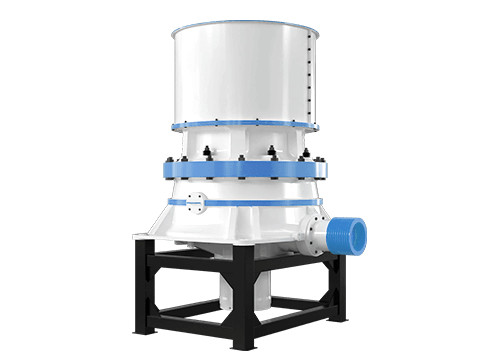
Cone Crusher
Employs interparticle crushing (also called layer compression), where rocks are crushed between a rotating mantle and a concave liner. The eccentric gyratory motion of the mantle creates a compressive force field, inducing fractures along grain boundaries.
Learn more >>
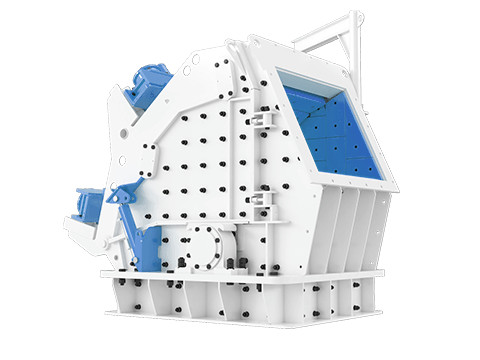
Impact Crusher
Dynamic Impact Crushing: Relies on kinetic energy transfer via high-speed rotors equipped with blow bars or hammers. Material is shattered by direct impact against rotating components or stationary anvils, with secondary fragmentation occurring through particle-on-particle collisions.
Learn more >>
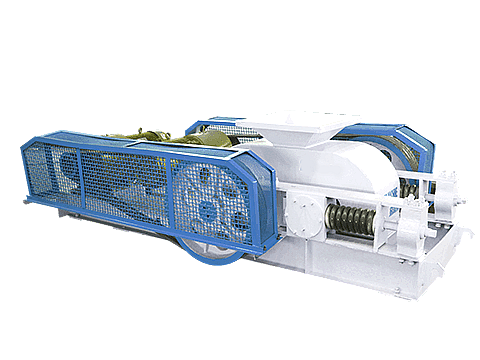
Roll Crusher
Shear-Compression Crushing: Applies shear-compression forces between counter-rotating rolls with textured or smooth surfaces. Material is drawn into the gap (nip angle) and fragmented via tensile failure or surface abrasion.
Learn more >>
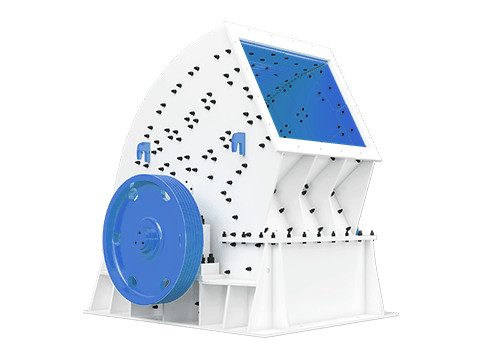
Hammer Crusher
Dynamic Impact with Grinding: Combines high-velocity hammer strikes (rotating hammers on a horizontal shaft) with material grinding against breaker plates or screens. Fragmentation occurs through impact, attrition, and shear.
Learn more >>
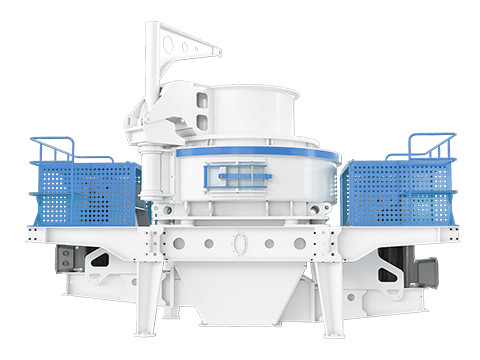
VSI Crusher
Centrifugal Acceleration Crushing: Accelerates material through a high-speed rotor (up to 70 m/s) and projects it against a stationary anvil or rock-lined chamber, exploiting centrifugal force and interparticle collision for fragmentation.
Learn more >>
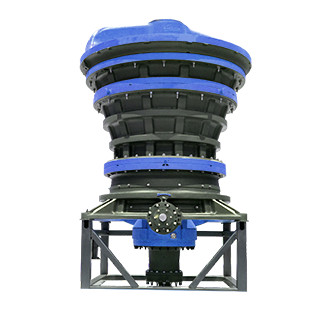
Gyratory Crusher
Conical Compression Crushing: Operates via a conical head gyrating within a concave bowl, generating progressive compression as material moves downward. Combines elements of jaw and cone crushers for ultra-high-capacity primary crushing.
Learn more >>
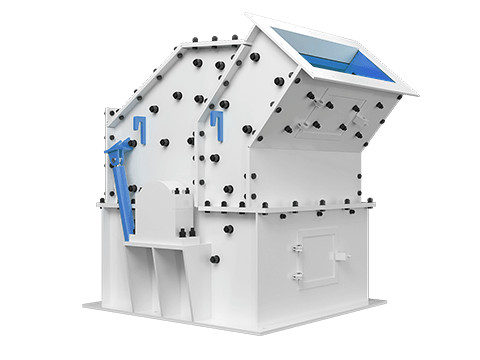
Fine Crusher
Fine Crusher is engineered for reliable and stable operation, making it an ideal choice for fine crushing applications across various industries.
Learn more >>
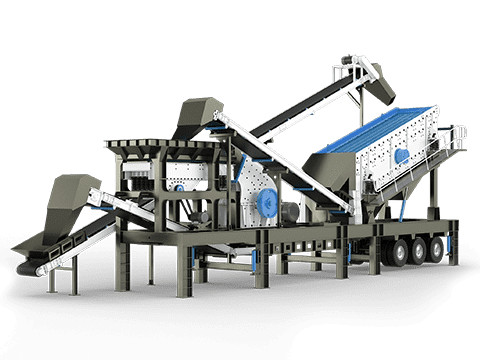
Mobile Crusher
The Mobile Crusher is designed to operate as a primary or secondary unit, making it a versatile choice for various applications.
Learn more >>