VSI Crusher
Centrifugal Acceleration Crushing: Accelerates material through a high-speed rotor (up to 70 m/s) and projects it against a stationary anvil or rock-lined chamber, exploiting centrifugal force and interparticle collision for fragmentation.
Main Components of VSI Crusher
VSI Crusher Types
Maintenance of VSI Crushers
Proper maintenance of VSI (Vertical Shaft Impact) crushers is essential to ensure optimal performance, longevity, and minimal downtime. Regular inspections, timely replacements, and adherence to best practices help maximize efficiency and reduce operational costs.
Regular Inspection and Monitoring
Routine inspections help identify potential issues before they lead to significant breakdowns. Operators should check for unusual vibrations, noise, and any signs of wear on critical components such as the rotor, bearings, and crushing chamber.
Lubrication System Maintenance
Proper lubrication is crucial for the smooth operation of VSI crushers. The lubrication system should be regularly checked, and oil levels must be maintained at the recommended levels. Using high-quality lubricants prevents excessive friction and extends the lifespan of moving parts.
Rotor and Wear Parts Replacement
The rotor is a critical component in VSI crushers, and its condition directly affects performance. Worn-out or unbalanced rotors should be replaced promptly. Additionally, wear parts such as anvils, shoes, and liners must be inspected and changed when necessary.
Monitoring Feed Material
Feeding the crusher with appropriate material size and type ensures smooth operation. Oversized or uncrushable materials can cause excessive wear and damage to internal components. A consistent and controlled feed rate improves efficiency and reduces wear.
Checking Belt Tension and Drive System
The belt and drive system should be inspected regularly to ensure proper tension and alignment. Loose or misaligned belts can cause inefficiencies and unexpected breakdowns. Keeping the drive system in good condition minimizes energy loss and ensures consistent power transmission.
Cleaning and Dust Control
Accumulated dust and debris can negatively impact VSI crusher performance. Regular cleaning of the machine, especially around the motor, bearings, and ventilation areas, helps prevent overheating and component failure.
Inspecting the Crushing Chamber
The crushing chamber should be checked for material buildup and excessive wear. Any blockages or uneven wear can affect crushing efficiency. Keeping the chamber clean and in good condition helps maintain consistent output quality.
Checking Safety Mechanisms
Safety systems such as automatic shut-off mechanisms, emergency stops, and overload protection should be tested periodically. Ensuring these features function correctly helps prevent accidents and damage to the machine.
Scheduled Preventive Maintenance
Following a structured preventive maintenance schedule helps avoid unexpected breakdowns. Manufacturers typically provide maintenance guidelines that should be followed to ensure long-term reliability and efficiency.
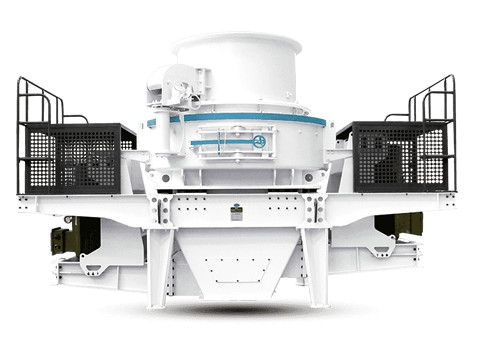
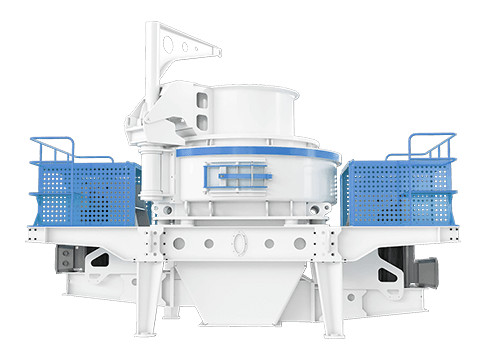
Applications of VSI Crushers
VSI (Vertical Shaft Impact) crushers are widely used in various industries due to their ability to produce high-quality, well-shaped aggregates and finely crushed materials. Their unique crushing mechanism makes them ideal for numerous applications, from construction to mining and industrial material processing.
Production of Manufactured Sand
VSI crushers are extensively used in the production of manufactured sand. They efficiently crush rocks into fine particles, creating high-quality sand that meets the specifications for concrete, asphalt, and other construction materials. Their ability to shape particles makes them a preferred choice for sand production.
Shaping Aggregates
One of the primary applications of VSI crushers is improving the shape of aggregates. These crushers reduce flaky and elongated particles, resulting in well-graded and cubical aggregates that enhance the strength and durability of concrete and asphalt mixtures.
Crushing Hard and Abrasive Materials
VSI crushers are effective in processing hard and abrasive materials such as granite, basalt, and quartz. Their high-speed impact crushing mechanism breaks down tough materials efficiently, making them suitable for mining and mineral processing industries.
Recycling and Waste Management
In recycling applications, VSI crushers are used to process construction and demolition waste, turning materials like concrete and asphalt into reusable aggregates. They help reduce landfill waste and promote sustainable construction practices.
Industrial Minerals Processing
VSI crushers are used in processing industrial minerals such as limestone, silica, and feldspar. Their fine crushing capability ensures consistent particle size distribution, making them valuable in industries like ceramics, glass manufacturing, and chemical processing.
Metallurgical Applications
In the metallurgical industry, VSI crushers help refine raw ores by reducing them to the desired particle size. They play a crucial role in ore beneficiation processes, enhancing the efficiency of subsequent grinding and separation stages.
Highway and Road Construction
VSI crushers contribute to highway and road construction by producing high-quality aggregates for asphalt and concrete pavements. Their ability to generate well-shaped particles improves road durability and reduces maintenance costs.
Artificial Rock Formation
VSI crushers are also used in landscaping and artificial rock formation projects. Their ability to create specific particle sizes and textures makes them suitable for decorative stone production and engineered landscapes.
How to Choose the Right VSI Crushers?
Choosing the right VSI (Vertical Shaft Impact) crusher is essential for achieving optimal performance, efficiency, and product quality. With various models available, selecting the best VSI crusher depends on factors such as application requirements, feed material characteristics, and production capacity. A well-chosen VSI crusher ensures consistent output, minimal downtime, and cost-effective operation.
Understanding the Application
The first step in selecting a VSI crusher is understanding the specific application. VSI crushers are commonly used for shaping aggregates, producing manufactured sand, and processing minerals. If the goal is to create fine, uniform particles, a high-speed VSI crusher may be the best option. For harder materials, a VSI with reinforced wear parts may be more suitable.
Considering Feed Material
The type and size of the feed material play a crucial role in choosing the right VSI crusher. Some VSI models are better suited for handling soft to medium-hard materials, while others can efficiently crush harder stones. The moisture content, abrasiveness, and friability of the material should also be considered to prevent excessive wear and maintain high efficiency.
Evaluating Rotor Speed and Configuration
The rotor is the heart of a VSI crusher, and its speed and configuration affect the crushing process. High-speed rotors produce finer particles, while lower-speed rotors generate coarser output. Some VSI crushers offer adjustable rotor speeds, allowing for more flexibility in controlling the final product shape and size.
Assessing Production Capacity
The required production capacity is another critical factor when choosing a VSI crusher. Different models offer varying throughput levels, so selecting a crusher that meets production demands without overloading the system ensures efficient operation. A VSI crusher with a well-matched motor and drive system will optimize energy consumption and reduce operational costs.
Evaluating Energy Efficiency
Energy consumption is a key consideration when selecting a VSI crusher. Modern VSI crushers incorporate advanced designs to minimize energy usage while maintaining high crushing efficiency. Choosing an energy-efficient model reduces operational costs and supports sustainable production.
Considering Maintenance Requirements
Maintenance needs should also be taken into account when selecting a VSI crusher. Some models offer easy access to wear parts and quick replacement mechanisms, reducing downtime. Selecting a crusher with durable components and a reliable lubrication system ensures long-term performance with minimal maintenance.
Comparing Different VSI Crusher Types
There are various sub-kinds of VSI crushers, including standard models, high-speed versions, and hybrid designs with hydraulic systems. Each type has unique features suited for different applications. Comparing different options based on operational needs helps in choosing the most suitable VSI crusher.
Budget and Cost Considerations
While the initial investment in a VSI crusher is important, long-term operating costs should also be considered. Factors such as wear part replacement frequency, energy consumption, and maintenance expenses impact overall costs. Choosing a VSI crusher with a balance between price and performance ensures a cost-effective solution.
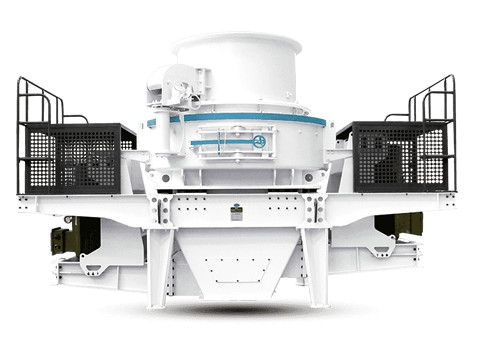
Stone Crusher Types
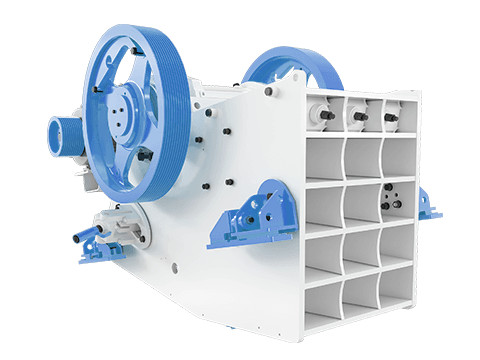
Jaw Crusher
Compressive Crushing: Utilizes compressive force generated by a reciprocating motion between a fixed jaw plate and a movable jaw plate. The material is crushed by progressive compression as it moves downward through the crushing chamber.
Learn more >>
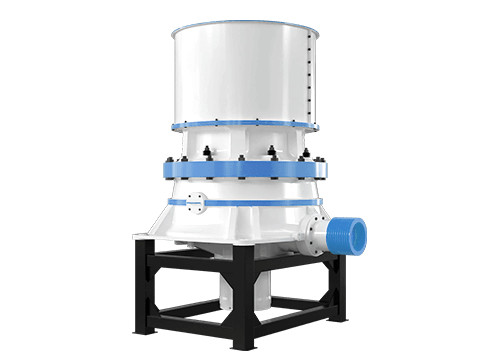
Cone Crusher
Employs interparticle crushing (also called layer compression), where rocks are crushed between a rotating mantle and a concave liner. The eccentric gyratory motion of the mantle creates a compressive force field, inducing fractures along grain boundaries.
Learn more >>
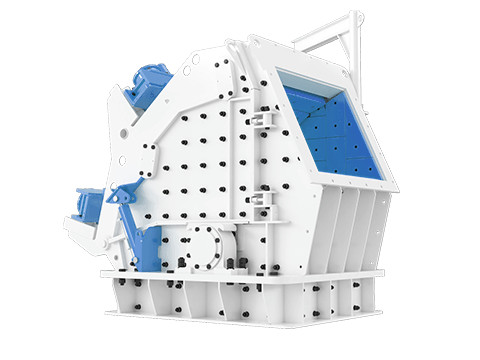
Impact Crusher
Dynamic Impact Crushing: Relies on kinetic energy transfer via high-speed rotors equipped with blow bars or hammers. Material is shattered by direct impact against rotating components or stationary anvils, with secondary fragmentation occurring through particle-on-particle collisions.
Learn more >>
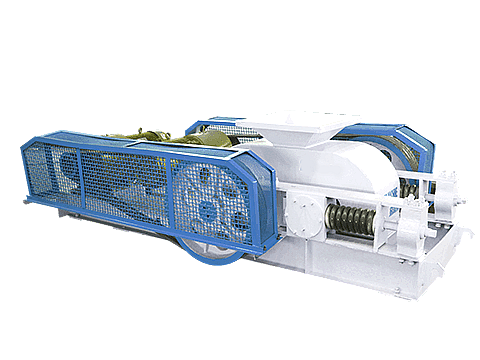
Roll Crusher
Shear-Compression Crushing: Applies shear-compression forces between counter-rotating rolls with textured or smooth surfaces. Material is drawn into the gap (nip angle) and fragmented via tensile failure or surface abrasion.
Learn more >>
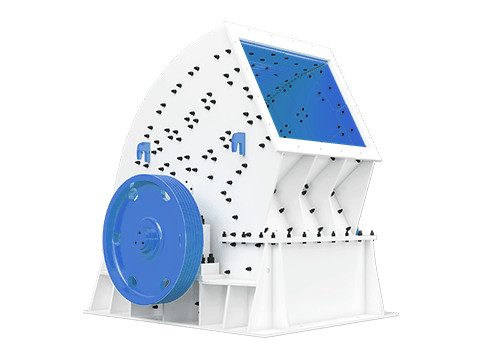
Hammer Crusher
Dynamic Impact with Grinding: Combines high-velocity hammer strikes (rotating hammers on a horizontal shaft) with material grinding against breaker plates or screens. Fragmentation occurs through impact, attrition, and shear.
Learn more >>
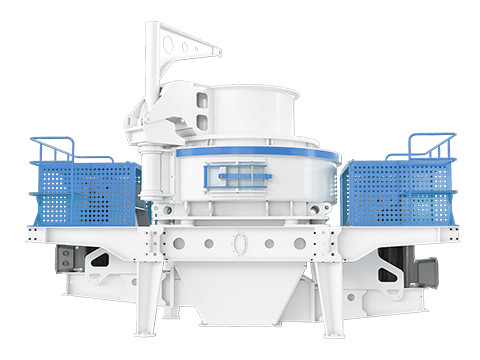
VSI Crusher
Centrifugal Acceleration Crushing: Accelerates material through a high-speed rotor (up to 70 m/s) and projects it against a stationary anvil or rock-lined chamber, exploiting centrifugal force and interparticle collision for fragmentation.
Learn more >>
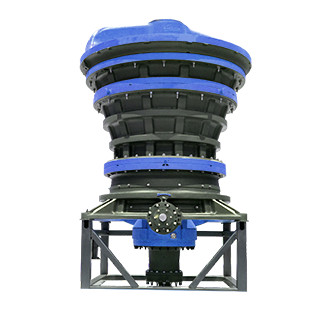
Gyratory Crusher
Conical Compression Crushing: Operates via a conical head gyrating within a concave bowl, generating progressive compression as material moves downward. Combines elements of jaw and cone crushers for ultra-high-capacity primary crushing.
Learn more >>
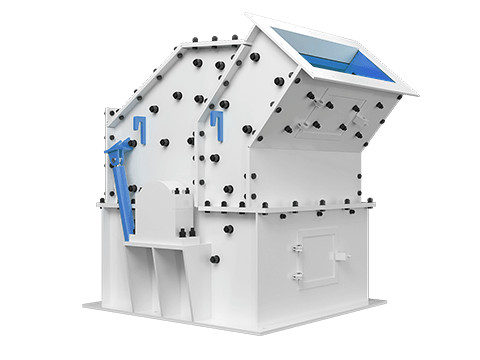
Fine Crusher
Fine Crusher is engineered for reliable and stable operation, making it an ideal choice for fine crushing applications across various industries.
Learn more >>
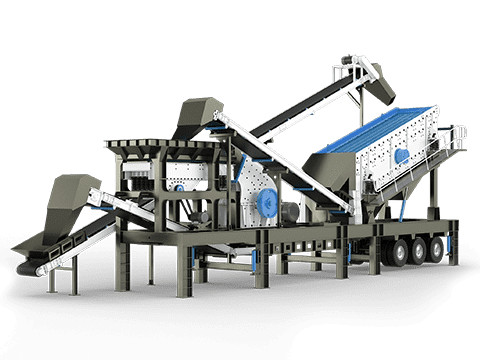
Mobile Crusher
The Mobile Crusher is designed to operate as a primary or secondary unit, making it a versatile choice for various applications.
Learn more >>